Jointing Metal with Brazing and Welding
There are several methods available for joining metals, including welding, brazing and soldering. What is the difference between welding and brazing? What is the difference between brazing and soldering? Let’s explore the distinctions plus comparative advantages as well as common applications. This discussion will deepen your understanding of metal joining and help you identify the optimal approach for your application.
HOW BRAZING WORKS
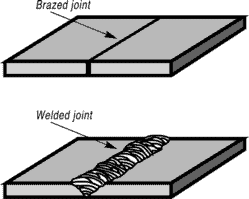
A
brazed joint is made in a completely different manner from a welded joint. The first big difference is in temperature – brazing does not melt the base metals. This means that brazing temperatures are invariably lower than the melting points of the base metals. Brazing temperatures are also significantly lower than welding temperatures for the same base metals, using less energy.
If brazing doesn’t fuse the base metals, how does it join them? It works by creating a metallurgical bond between the filler metal and the surfaces of the two metals being joined. The principle by which the filler metal is drawn through the joint to create this bond is capillary action. In a brazing operation, you apply heat broadly to the base metals. The filler metal is then brought into contact with the heated parts. It is melted instantly by the heat in the base metals and drawn by capillary action completely through the joint. This is how a brazed joint is made.
Brazing applications include electronics/electrical, aerospace, automotive, HVAC/R, construction and more. Examples range from air conditioning systems for automobiles to highly sensitive jet turbine blades to satellite components to fine jewelry. Brazing offers a significant advantage in applications that require joining of dissimilar base metals, including copper and steel as well as non-metals such as tungsten carbide, alumina, graphite and diamond.
Comparative Advantages. First, a brazed joint is a strong joint. A properly made brazed joint (like a welded joint) will in many cases be as strong or stronger than the metals being joined. Second, the joint is made at relatively low temperatures, ranging from about 1150°F to 1600°F (620°C to 870°C).
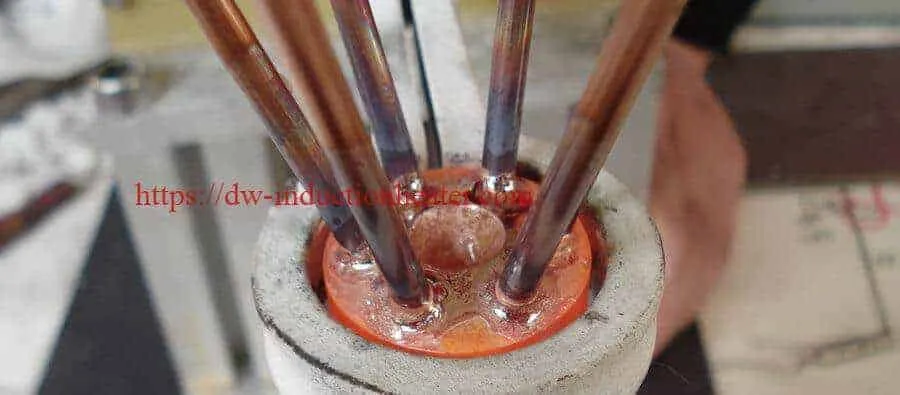
Most significant, the base metals are never melted. Since the base metals are not melted, they can typically retain most of their physical properties. This base metal integrity is characteristic of all brazed joints, including both thin- and thick-section joints. Also, the lower heat minimizes danger of metal distortion or warping. Consider too, that lower temperatures require less heat – a significant cost-saving factor.
Another important advantage of brazing is the ease of joining dissimilar metals using flux or flux-cored/coated alloys. If you don’t have to melt the base metals to join them, it doesn’t matter if they have widely different melting points. You can braze steel to copper as easily as steel to steel. Welding is a different story because you must melt the base metals to fuse them. This means that if you try to weld copper (melting point 1981°F/1083°C) to steel (melting point 2500°F/1370°C), you must employ rather sophisticated and expensive welding techniques. The total ease of joining dissimilar metals through conventional brazing procedures means you can select whatever metals are best suited to the function of the assembly, knowing you’ll have no problem joining them no matter how widely they vary in melting temperatures.
Also, a
brazed joint has a smooth, favorable appearance. There is a night-and-day comparison between the tiny, neat fillet of a brazed joint and the thick, irregular bead of a welded joint. This characteristic is especially important for joints on consumer products, where appearance is critical. A brazed joint can almost always be used “as is,” without any finishing operations needed – another cost savings.
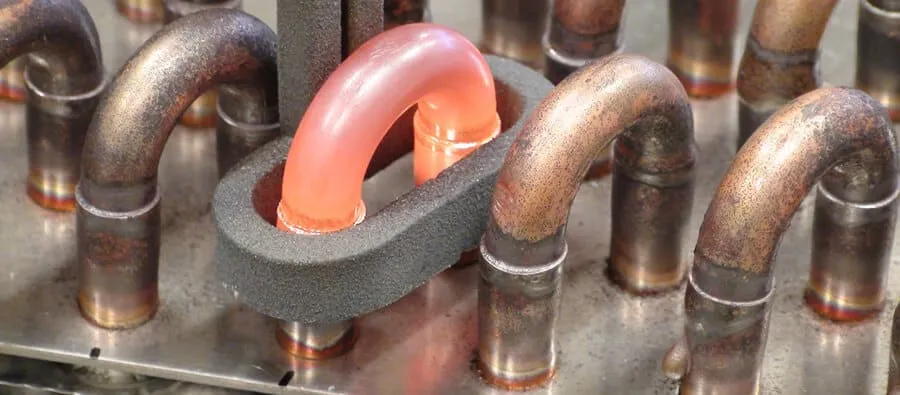
Brazing offers another significant advantage over welding in that operators can usually acquire brazing skills faster than welding skills. The reason lies in the inherent difference between the two processes. A linear welded joint must be traced with precise synchronization of heat application and deposition of filler metal. A brazed joint, on the other hand, tends to “make itself” through capillary action. In fact, a considerable portion of the skill involved in brazing is rooted in the design and engineering of the joint. The comparative speed of highly skilled operator training is an important cost factor.
Finally,
metal brazing is relatively easy to automate. The characteristics of the brazing process – broad heat applications and ease of filler metal positioning – help eliminate the potential for problems. There are many ways to heat the joint automatically, many forms of brazing filler metal and many ways to deposit them so that a brazing operation can easily be automated for almost any level of production.
HOW WELDING WORKS
Welding joins metals by melting and fusing them together, typically with the addition of a welding filler metal. The joints produced are strong – usually as strong as the metals joined, or even stronger. To fuse the metals, you apply a concentrated heat directly to the joint area. This heat must be of a high temperature to melt the base metals (the metals being joined) and the filler metals. Therefore, welding temperatures start at the melting point of the base metals.
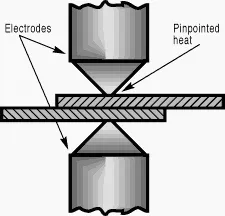
Welding is generally suited to joining large assemblies where both metal sections are relatively thick (0.5”/12.7mm) and joined at a single point. Since the bead of a welded joint is irregular, it is not typically used in products requiring cosmetic joints. Applications include transportation, construction, manufacturing and repair shops. Examples are robotic assemblies plus fabrication of pressure vessels, bridges, building structures, aircraft, railway coaches and tracks, pipelines and more.
Comparative Advantages. Because welding heat is intense, it is typically localized and pinpointed; it is not practical to apply it uniformly over a broad area. This pinpointed aspect has its advantages. For example, if you want to join two small strips of metal at a single point, an electrical resistance welding approach is practical. This is a fast, economical way to make strong, permanent joints by the hundreds and thousands.
If the joint is linear rather than pinpointed, though, problems arise. The localized heat of welding can become a disadvantage. For example, if you want to butt-weld two pieces of metal, you begin by beveling the edges of the metal pieces to allow room for the welding filler metal. Then you weld, first heating one end of the joint area to melting temperature, then slowly moving the heat along the joint line, depositing filler metal in synchronization with the heat. This is a typical, conventional welding operation. Properly made, this welded joint is at least as strong as the metals joined.
However, there are disadvantages to this linear-joint-welding approach. The joints are made at high temperatures – high enough to melt both base metals and filler metal. These high temperatures can cause problems, including possible distortion and warping of the base metals or stresses around the weld area. These dangers are minimal when the metals being joined are thick, but they may become problems when the base metals are thin sections. Also, high temperatures are expensive, since heat is energy and energy costs money. The more heat you need to make the joint, the more the joint will cost to produce.

Now, consider the automated welding process. What happens when you join not one assembly, but hundreds or thousands of assemblies? Welding, by its nature, presents problems in automation. A resistance-weld joint made at a single point is relatively easy to automate. However, once the point becomes a line – a linear joint – once again, the line must be traced. It's possible to automate this tracing operation, moving the joint line, for example, past a heating station and feeding filler wire automatically from big spools. This is a complex and exacting setup, though, warranted only when you have large production runs of identical parts.
Keep in mind that welding techniques do continually improve. You can weld on a production basis via electron beam, capacitor discharge, friction and other methods. These sophisticated processes usually call for specialized and expensive equipment plus complex, time consuming setups. Consider if they are practical for shorter production runs, changes in assembly configuration or typical day-to-day metal joining requirements.
Choosing the Right Metal Joining Process
If you need joints that are both permanent and strong, you will likely narrow down your metal joining consideration to welding versus
brazing. Welding and brazing both use heat and filler metals.

They can both be performed on a production basis. However, the resemblance ends there. They work differently, so remember these brazing vs welding considerations:
Size of the assembly
Thickness of the base metal sections
Spot or line joint requirements
Metals being joined
Final assembly quantity needed
Other options? Mechanically fastened joints (threaded, staked or riveted) generally don’t compare to brazed joints in strength, resistance to shock and vibration, or leak-tightness. Adhesive bonding and soldering will provide permanent bonds, but generally, neither can offer the strength of a brazed joint –equal to or greater than that of the base metals themselves. Nor can they, as a rule, produce joints that offer resistance to temperatures above 200°F (93°C). When you need permanent, robust metal-to-metal joints, brazing is a strong contender.