Induction Stress Relieving: A Comprehensive Guide
Induction stress relieving is a highly effective method for reducing residual stresses in metal components, resulting in improved durability and performance. This process uses electromagnetic induction to heat the material, allowing for controlled and uniform stress relief without the risk of distortion or damage. With its ability to enhance the mechanical properties of metal parts, induction stress relieving is a crucial step in the manufacturing and maintenance of critical components across various industries.
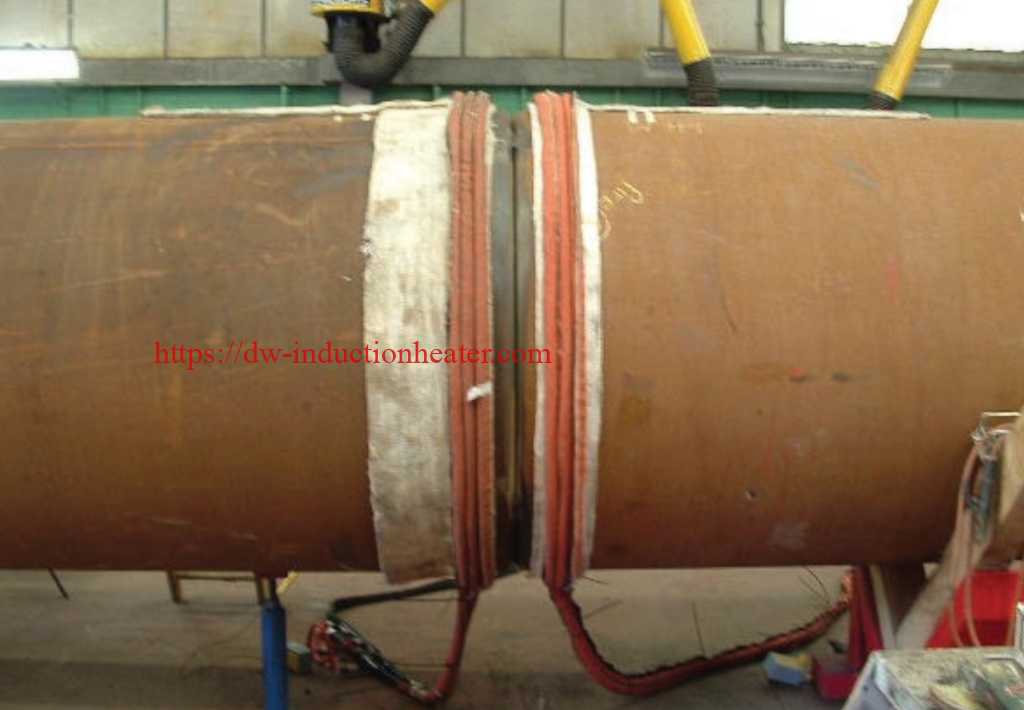
In today's fast-paced and demanding work environment, stress is a common occurrence for many individuals. Whether it's due to work-related pressures, personal issues, or a combination of both, stress can have a significant impact on an individual's overall well-being and productivity. As a result, finding effective ways to manage and alleviate stress has become increasingly important.
One method that has gained popularity in recent years is induction stress relieving. This technique uses electromagnetic induction to heat metal components to a specific temperature and then slowly cool them down, resulting in the reduction of internal stresses within the material. In this comprehensive guide, we will explore the principles behind induction stress relieving, its applications in various industries, and the benefits it offers for individuals and organizations.
Principles of Induction Stress Relieving
Induction stress relieving is based on the principle of thermal expansion and contraction. When metal components are heated to a specific temperature, their molecules become more mobile, allowing internal stresses to be redistributed and reduced. As the components are slowly cooled down, the molecules return to their original positions in a more relaxed state, resulting in reduced internal stresses.
The process of induction stress relieving involves using an induction heating system to generate an alternating magnetic field around the metal components. This magnetic field induces eddy currents within the material, causing it to heat up rapidly. By controlling the frequency and power of the induction heating system, precise temperatures can be achieved to effectively relieve internal stresses within the metal components.
Applications of Induction Stress Relieving
Induction stress relieving has found widespread applications across various industries due to its effectiveness in reducing internal stresses within metal components. Some common applications include:
- Welded assemblies: Welding processes often introduce significant internal stresses within metal components due to rapid heating and cooling cycles. Induction stress relieving can be used to alleviate these stresses and improve the overall integrity of welded assemblies.
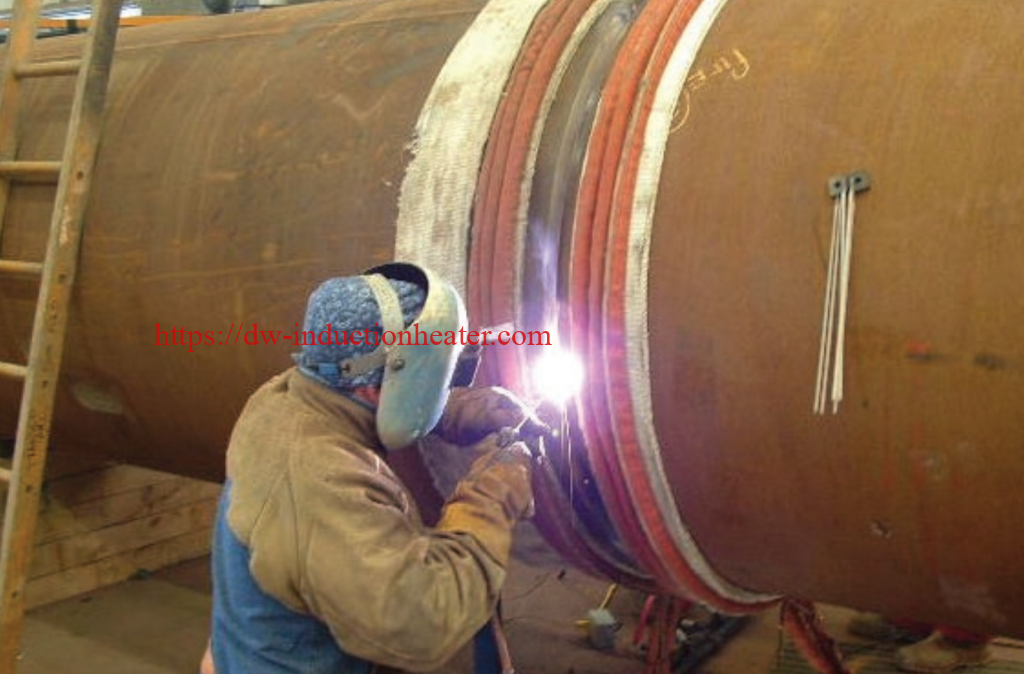
- Machined parts: Metal parts that undergo machining processes such as milling or turning can develop residual stresses that affect their dimensional stability and performance. Induction stress relieving can help mitigate these issues and improve the quality of machined parts.
- Castings: Casting processes can result in uneven cooling rates within metal castings, leading to internal stresses that affect their mechanical properties. Induction stress relieving can help homogenize these stresses and improve the overall quality of castings.
- Heat-treated components: Heat treatment processes such as quenching or tempering can introduce residual stresses within metal components. Induction stress relieving can be used as a post-treatment step to reduce these residual stresses and improve the overall stability of heat-treated components.
Benefits of Induction Stress Relieving
The use of induction stress relieving offers several key benefits for individuals and organizations:
- Improved mechanical properties: By reducing internal stresses within metal components, induction stress relieving can improve their mechanical properties such as strength, ductility, and fatigue resistance.
- Enhanced dimensional stability: Internal stresses within metal components can lead to dimensional instability over time. Induction stress relieving helps mitigate these issues by promoting dimensional stability and reducing distortion.
- Increased product reliability: Components that undergo induction stress relieving are less prone to premature failure due to reduced internal stresses, resulting in increased product reliability and longevity.
- Improved performance: Induction stress relieving can help improve the performance of components by reducing internal stresses, which can lead to better dimensional stability and overall performance.
- Cost savings: By reducing the likelihood of premature failure and the need for frequent repairs or replacements, induction stress relieving can result in cost savings for manufacturers and end users.
- Enhanced safety: Components that undergo induction stress relieving are less likely to fail unexpectedly, which can enhance overall safety in various applications.
- Better quality control: Induction stress relieving can help manufacturers maintain better quality control by ensuring that components are free from excessive internal stresses that could compromise their performance or reliability.
Mastering Induction Stress Relieving for Improved Product Performance
Induction stress relieving is a crucial process in the manufacturing industry that can significantly improve the performance of products. By subjecting metal components to controlled heating and cooling cycles, induction stress relieving helps to reduce internal stresses and improve the overall stability and durability of the product.
To master induction stress relieving for improved product performance, it is essential to understand the principles behind the process and how it can benefit different types of materials and components. Here are some key steps to consider:
1. Understand the Material Properties: Different materials have unique properties that influence how they respond to stress relieving processes. It's important to have a thorough understanding of the material being used and how it will react to induction heating.
2. Determine Optimal Parameters: The success of induction stress relieving depends on using the right combination of temperature, time, and cooling rates. It's crucial to determine the optimal parameters for each specific application to achieve the desired results.
3. Use Advanced Induction Heating Equipment: Investing in high-quality induction heating equipment is essential for achieving precise control over the stress relieving process. Advanced technology allows for accurate temperature monitoring and uniform heating, resulting in consistent and reliable outcomes.
4. Implement Quality Control Measures: To ensure that induction stress relieving is effectively reducing internal stresses, it's important to implement quality control measures such as non-destructive testing and inspection techniques.
5. Continuously Improve Processes: Mastering induction stress relieving requires a commitment to continuous improvement. By analyzing data, gathering feedback, and making adjustments as needed, manufacturers can refine their processes for optimal results.
By mastering induction stress relieving techniques, manufacturers can enhance product performance by reducing distortion, improving dimensional stability, and increasing resistance to fatigue and corrosion. This ultimately leads to higher-quality products with improved reliability and longevity in service.
In conclusion, mastering
induction stress relieving is essential for achieving improved product performance in manufacturing. By understanding material properties, determining optimal parameters, using advanced equipment, implementing quality control measures, and continuously improving processes, manufacturers can harness the full potential of this critical heat treatment technique.
https://dw-inductionheater.com/induction-stress-relieving-a-comprehensive-guide.html?feed_id=231114&_unique_id=656884774387c