Achieving High-Quality Tooth-by-Tooth Hardening of Large Gears with Induction Heating

In the manufacturing industry, large gears play a critical role in various applications such as heavy machinery, wind turbines, and industrial equipment. To ensure their durability and performance, it is essential to apply a hardening process to the gear teeth. One of the most effective methods for achieving tooth-by-tooth hardening in large gears is through induction heating.
Induction heating is a process that utilizes electromagnetic induction to heat the surface of the gear teeth rapidly. By applying a high-frequency alternating current to a coil, a magnetic field is generated, which induces eddy currents in the gear tooth surface. These eddy currents create localized heating, allowing for precise and controlled hardening of each individual tooth.
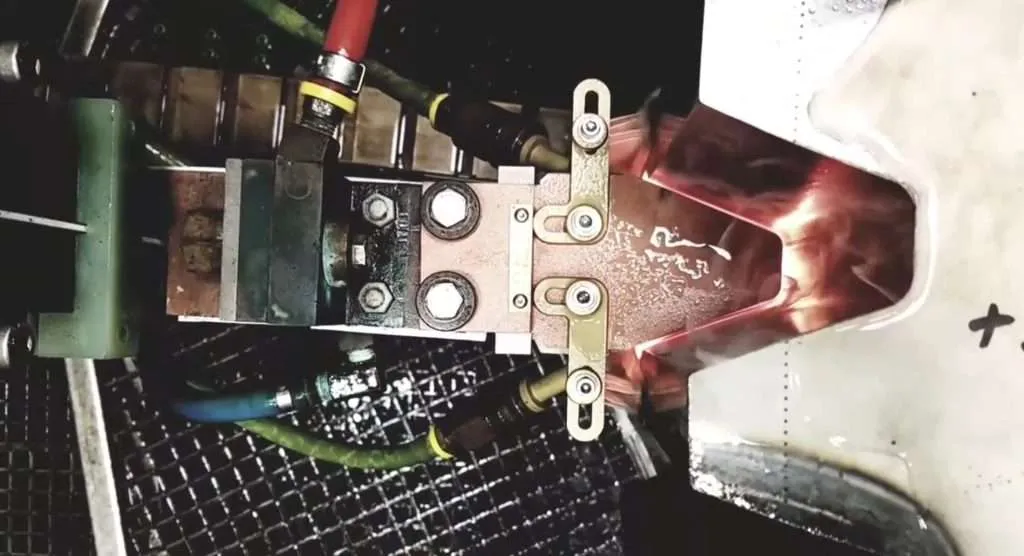
Tooth-by-tooth hardening using induction heating offers several advantages over other hardening methods. Firstly, it ensures uniform hardness distribution across the gear teeth, resulting in improved wear resistance and load-carrying capacity. This is particularly crucial for large gears that are subjected to heavy loads and harsh operating conditions.
Secondly, induction heating enables selective hardening, meaning only the gear teeth are heated, while the rest of the gear remains relatively unaffected. This minimizes the risk of distortion or warping, which can occur with other heat treatment methods that involve heating the entire gear. The precise control over the heating process allows for targeted hardening, resulting in a high-quality, dimensionally stable gear.
Induction hardening of small-, medium, and large-size gears is done using a tooth-by-tooth technique or encircling method. Depending on the gear size, required hardness pattern and geometry, gears are induction hardened by encircling the whole gear with a coil (so-called “spin hardening of gears”), or for larger gears, heating them “tooth-by-tooth”, where a more precise hardening result can be achieved, although the process is much slower.
Tooth-by-Tooth Hardening of large gears
The tooth-by-tooth method can be done in two alternative techniques:
“tip-by-tip” applies a single-shot heating mode or scanning mode, an inductor encircles a body of a single tooth. This method is rarely used because it does not provide the required fatigue and impact strength.
A more popular “gap-by-gap” hardening technique applies only a scanning mode. It requires the inductor to be symmetrically located between two flanks of adjacent teeth. Inductor scanning rates are typically within 6mm/sec to 9mm/sec.

There are two scanning techniques used:
- the inductor is stationary and the gear is moveable
- the gear is stationary and the inductor is moveable (more popular when hardening large-size gears)
The induction hardening Inductor
Inductor geometry depends upon the shape of the teeth and the required hardness pattern. Inductors can be designed to heat only the root and/or flank of the tooth, leaving the tip and tooth core soft, tough, and ductile.
Simulation helps prevent overheating
When developing tooth-by-tooth gear hardening processes, particular attention should be paid to electromagnetic end/edge effects and the ability to provide the required pattern in the gear end areas.
Upon scanning a gear tooth, the temperature is distributed within gear roots and flanks quite uniformly. At the same time, since the eddy current makes a return path through the flank and, particularly through the tooth tip, proper care should be taken to prevent overheating the tooth tip regions, in particular at the beginning and at the end of the scan hardening. A simulation can help to prevent these unwanted effects before developing the process.
Simulation example
Scanning tooth by tooth gear hardening case at 12 kHz.
Spray cooling is also simulated but not visible in the result images. A cooling effect is applied to the top and side faces of the two teeth, as well as moving the cooling zone following the inductor.
3D Hardened profile in grey color:
2D Hardened profile vertical slice: CENOS allows you to easily visualize how the hardened profile becomes deeper if the power is not decreased or switched off near the end of the gear. 
Current density on gear:
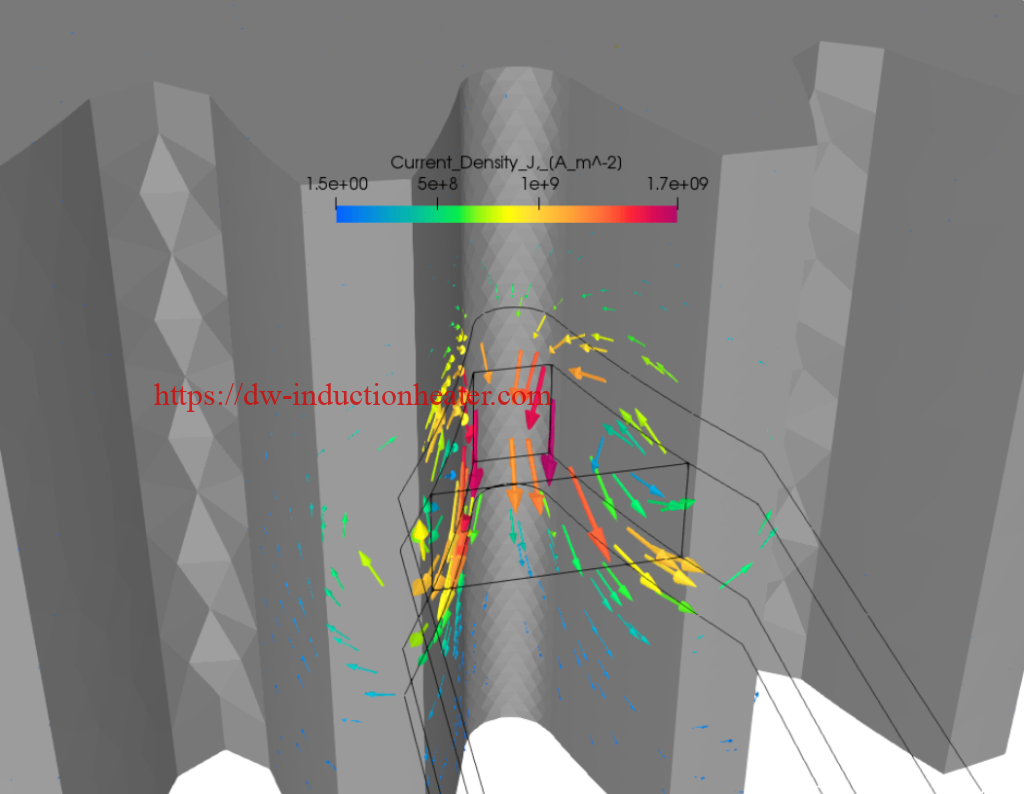
Additionally, induction heating offers rapid heating and cooling rates, reducing the overall processing time compared to conventional methods. This is particularly advantageous for large gears, as it helps to improve production efficiency and reduce costs.
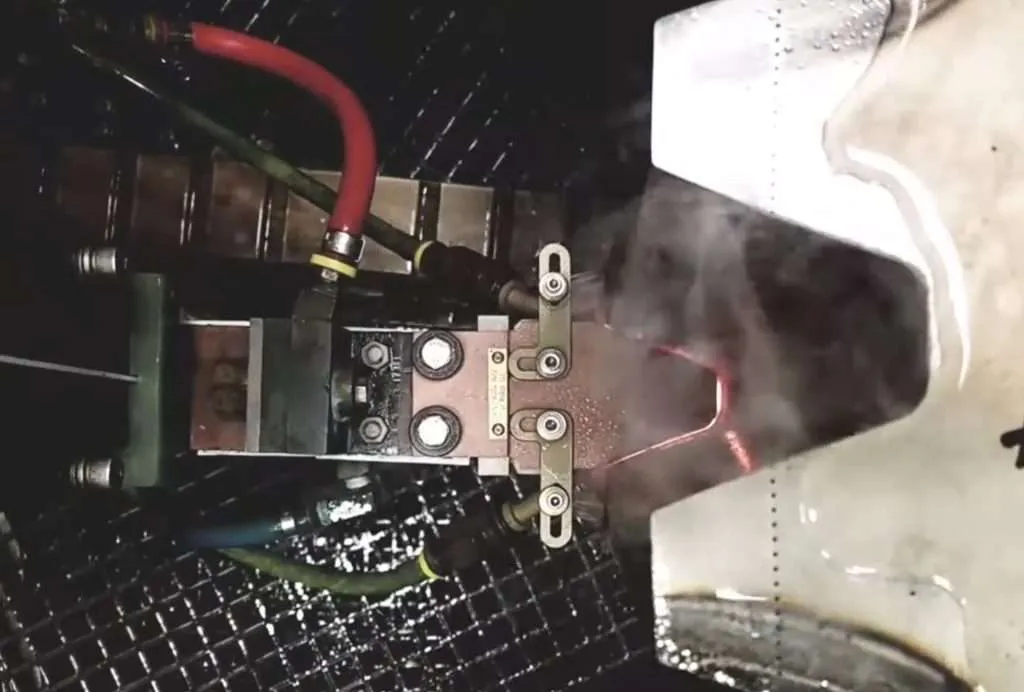
To achieve tooth-by-tooth hardening of large gears using induction heating, specialized equipment is required. The induction heating system typically consists of a power supply, a coil or inductor, and a cooling system. The gear is positioned in the coil, and the power supply is activated to generate the required heat. The process parameters, such as power, frequency, and heating time, are carefully controlled to achieve the desired hardness profile.
In conclusion, tooth-by-tooth hardening of large gears using induction heating is a highly effective and efficient method. It ensures uniform hardness distribution, selective hardening, and rapid processing times, resulting in high-quality, durable gears. If you are involved in the manufacturing of large gears, considering the implementation of induction heating for tooth-by-tooth hardening can significantly enhance the performance and longevity of your products.
https://dw-inductionheater.com/tooth-by-tooth-induction-scanning-hardening-teeth-of-large-gear.html?feed_id=231059&_unique_id=6565e6b017c2d