What is induction heat treating surface process?
Induction heating is a heat treating process that allows very targeted heating of metals by electromagnetic induction. The process relies on induced electrical currents within the material to produce heat and is the preferred method used to bond, harden or soften metals or other conductive materials. In modern manufacturing processes, this form of heat treatment offers a beneficial combination of speed, consistency and control. Although the basic principles are well known, modern advances in solid state technology have made the process remarkably simple, cost-effective heating method for applications which involve joining, treating, heating and materials testing.
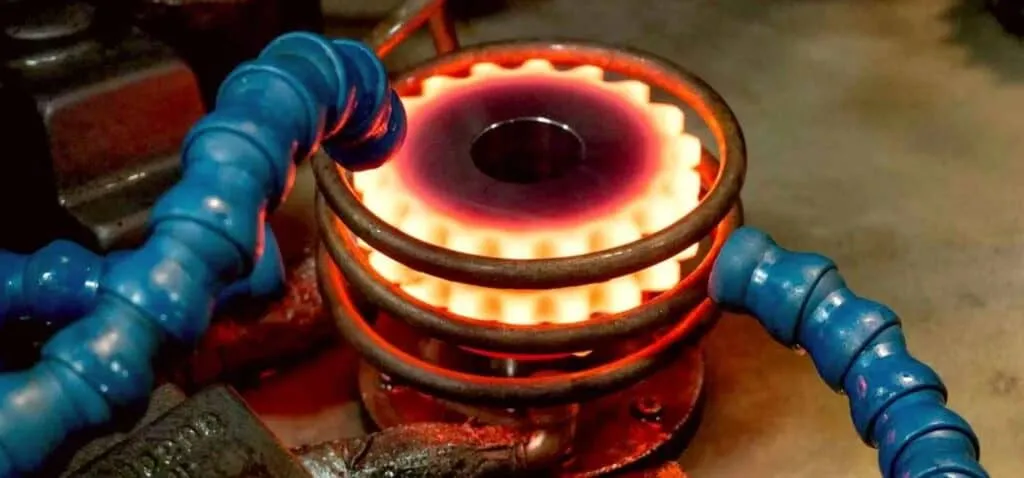
Induction heat treating, through the highly controllable use of an electrically heated coil, will allow you to select the best physical characteristics for not only each metal part—but for each section on that metal part. Induction hardening can impart superior durability to bearing journals and shaft sections without sacrificing the ductility necessary to handle shock loads and vibration. You can harden internal bearing surfaces and valve seats in intricate parts without creating distortion problems. This means that you are able to harden or anneal specific areas for durability and ductility in ways that will best serve your needs.
Benefits of Induction Heat Treating Services
- Focused Heat Treat Surface hardening retains original ductility of core while hardening a high wear area of the part. The hardened area is accurately controlled in respect to case depth, width, location and hardness.
- Optimized Consistency Eliminate the inconsistencies and quality issues associated with open flame, torch heating and other methods. Once the system is properly calibrated and set up, there is no guess work or variation; the heating pattern is repeatable and consistent. With modern solid state systems, precise temperature control provides uniform results.
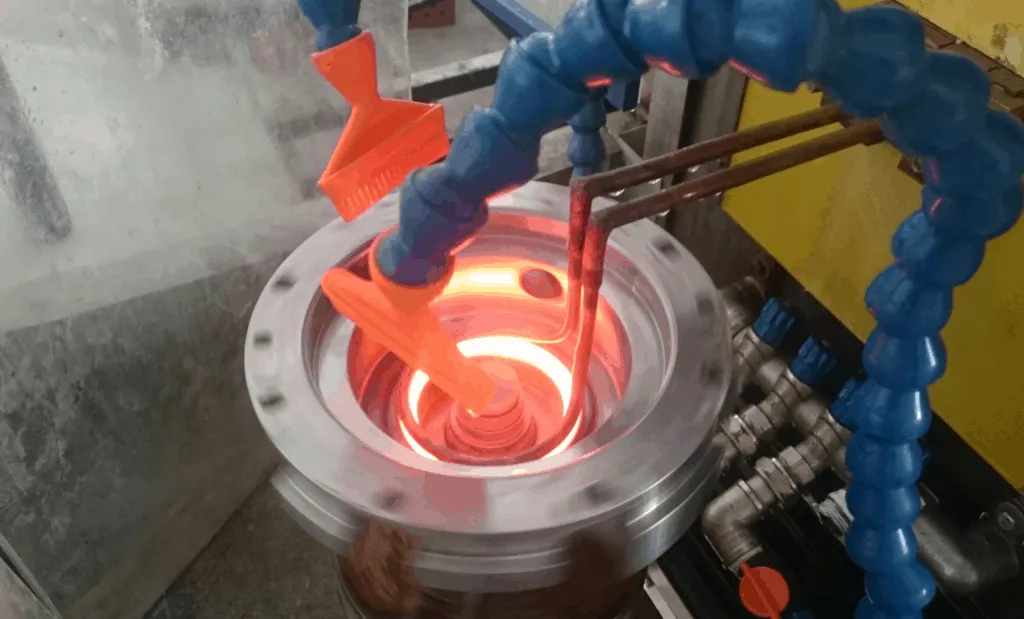
- Maximized Productivity Production rates can be maximized because heat is developed directly and instantly (>2000º F. in < 1 second) inside the part. Startup is virtually instantaneous; no warm up or cool down cycle is required.
- Improved Product Quality Parts never come into direct contact with a flame or other heating element; the heat is induced within the part itself by alternating electrical current. As a result, product warpage, distortion and reject rates are minimized.
- Reduced Energy Consumption Tired of increasing utility bills? This uniquely energy-efficient process converts up to 90% of the energy expended energy into useful heat; batch furnaces are generally only 45% energy-efficient. No warm-up or cool-down cycles are required so stand-by heat losses are reduced to a bare minimum.
- Environmentally Sound The burning of traditional fossil fuels is unnecessary, resulting in a clean, non-polluting process which will help protect the environment.
What is Induction Heating?
Induction Heating is a Contactless Heating Method of bodies, which absorb energy from an Alternating Magnetic Field, generated by Induction Coil (Inductor).
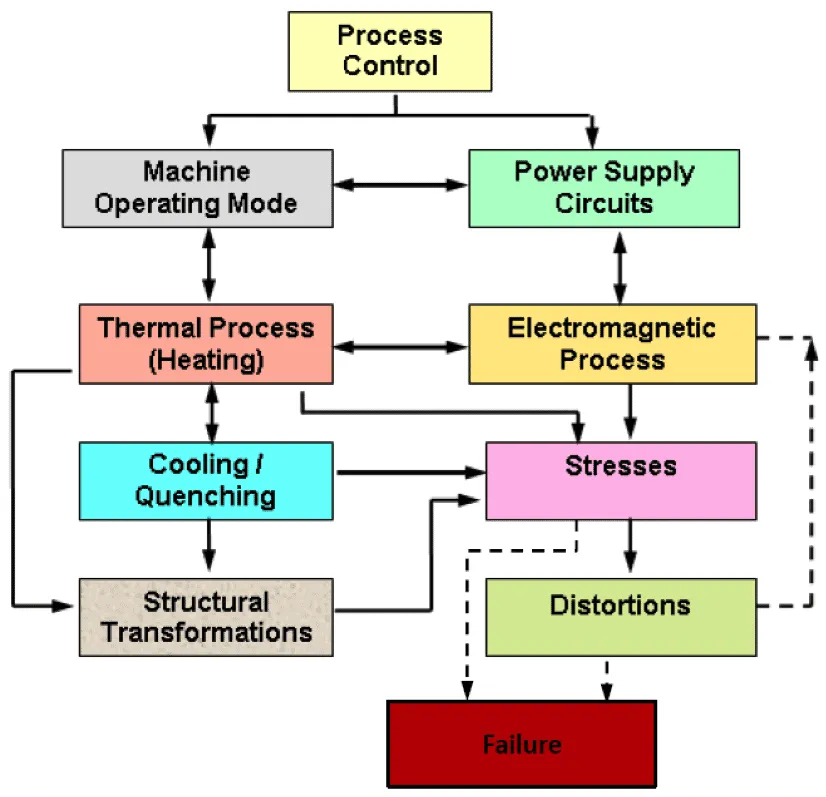
There are two mechanisms of energy absorption:
- generation of close-loop (eddy) currents inside the body which cause heating due to electrical resistance of the body material
- hysteresis heating (for magnetic materials ONLY!) due to a friction of magnetic micro volumes (domains), which rotate following orientation of external magnetic field
Principle of Induction Heating
Chain of phenomena:
- Induction heating power supply delivers current (I1) to induction coil
- Coil currents (ampere-turns) generate magnetic field. Lines of field are always closed (law of nature!) and each line goes around the current source – coil turns and workpiece
- Alternating magnetic field flowing through the part cross-section (coupled to the part) induces voltage in the part
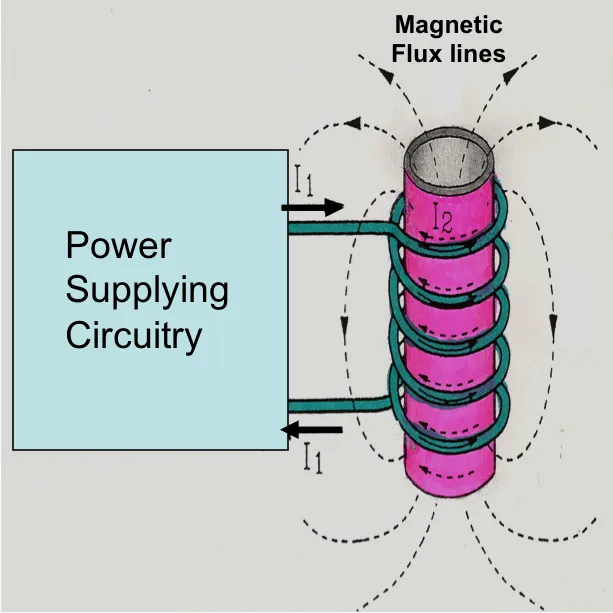
- Induced voltage creates eddy currents (I2) in the part flowing in direction opposite to the coil current where possible
- Eddy currents generate heat in the part
Power Flow in Induction Heating Installations
Alternating current changes direction twice during each frequency cycle. If frequency is 1kHz, current changes direction 2000 times in a second.
A product of current and voltage gives the value of instantaneous power (p = i x u), which oscillates between the power supply and the coil. We can say that power is being partially absorbed (Active Power) and partially reflected (Reactive Power) by the coil. Capacitor battery is used to unload the generator from the reactive power. Capacitors receive reactive power from the coil and send it back to the coil supporting oscillations.
A circuit “coil-transformer-capacitors” is called Resonant or Tank Circuit.
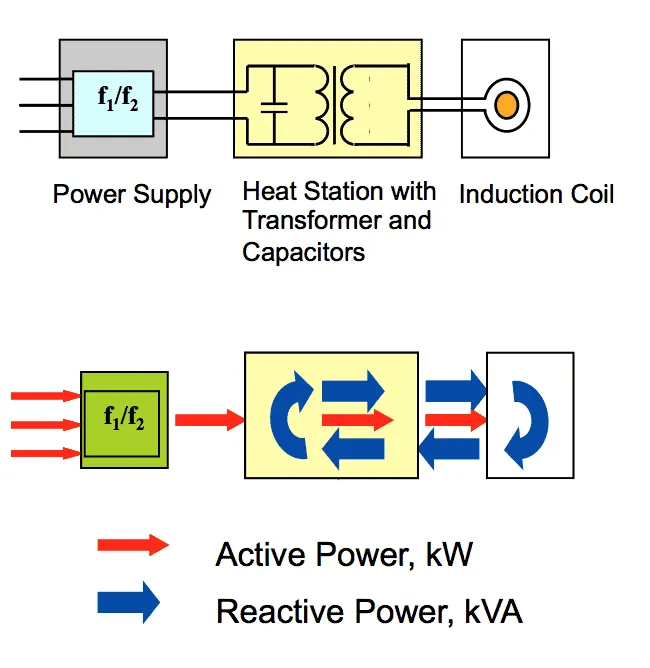