Brief Introduction of induction heating plastic extrusion:
Induction heating plastic extrusion is a one type of energy-saving heater. It has many advantages including significant energy-saving, fast heating up, high energy efficiency, low or zero maintenance etc. It can also lower environment temperature by generating much less heat. While installing the induction heater system, there will not involve any major changes to the electrical control system.
Where can induction heating plastic extrusion?
It is mainly applied to injection, extrusion; blow filming, wire drawing, granulating and recycling machines, etc. The product application includes film, sheet, profile, raw material etc. It can be used for heating the barrel, flange, die head, screw and other parts of the machines. It is excellent in energy-saving and cooling down work environment.
Induction heating is the process of heating an electrically conducting object (usually a metal) by electromagnetic induction, where eddy currents are generated within the metal and resistance leads to Joule heating of the metal. The induction coil itself does not get heated. The heat generating object is the heated object itself.
Why and how induction heating plastic extrusion can save energy?
Presently,most of the plastic machines are using the conventional resistance heating method, where the resistance wire is heated up and then transfer the heat to the barrel via heater cover.So only the heat close to the barrel surface can be transferred to the barrel and the heat close to outside heater cover is lost to the air which causes a rise in environment temperature. Induction heater is technology where high frequency magnetic fields which cause he be heated up bu electro-magnetic field(EMF)that are brushing against each other.When the barrel is heated up and heat is minimum,there is very high heat efficiency and minimum heat loss to the environment where energy saving could reach30-80%.Due to the fact that the induction coil is not producing any high heat and also there is no resistance wire that gets oxidized and causes the heater to burn out, the induction heater has a longer service life and also less maintenance.
What are the advantages of induction heating plastic extrusion?
- Energy efficiency 30%-85% Currently, plastic processing machinery mainly uses resistance heating elements which can produce a large amount of heat radiated to the surroundings. Induction heating is an ideal alternative to solve this issue. The surface temperature of induction heating coil ranges between 50ºC and 90ºC, the heat losses are significantly minimized, providing energy savings of 30%-85%. The energy saving effect is therefore more obvious when the induction heating system is used in high power heating equipment.
- Safety Using induction heating system enables the surface of the machine to be safe for touching, and that means it can avoid burn injuries which often occur in plastic machines that use resistance heating elements, providing a safe workplace for operators.
- Fast heating, high heating efficiency Compared to resistance heating whose energy conversion efficiency is approximately at 60%, the induction heating is over 98% efficient at converting electricity to heat.
- Lower workplace temperature, higher operation comfort After using induction heating system, the temperature of entire production workshop is lowered by more than 5 degrees.
- Long service life In contrast to resistance heating elements that have to long-lasting work at high temperature, the induction heating works at near ambient temperature, therefore efficiently prolonging the service life.
- Accurate temperature control, high product qualification rate The induction heating provides low or no thermal inertia, so that it will not cause the temperature overshoot. And the temperature can remain at set value of 0.5 degree difference.
What is the superiority of induction heating for plastic extrusion compared with traditional heaters?
Induction heater | Traditional heaters | |
Heating method | Induction heating is the process of heating an electrically conducting object (usually a metal) by electromagnetic induction, where eddy currents are generated within the metal and resistance leads to Joule heating of the metal. The induction coil itself does not get heated. The heat generating object is the heated object itself | Resistance wires get heated directly and heat is transferred by contact. |
heating up time | Quicker heating-up, higher efficiency | slower heating-up, lower efficiency |
Energy saving rate |
Save 30-80% energy rate,reduce working temperature |
Cannot save energy |
Installation | Easy to install | Easy to install |
Operation | Easy to operate | Easy to operate |
Maintenance |
Control box is easy to replace without turning off your machine |
Easy to replace but have to turning off your machine |
Temperature Control | Small thermal inertia and precise temperature control because the heater doesn’t get heated byitself. | Big thermal inertia, low accuracy in temperature control |
Product Quality | Higher product quality because of precise temperature control | Lower product quality |
Safety |
Outer sheath is safe to touch, lower surface temperature, no electric leakage. |
Temperature on outer sheath is much higher, easy to get burned. Electric leakage under wrong operation. |
Service life of heater | 2-4years | 1-2 years |
Service life of Barrel and Screw |
Longer usage life for barrel, screw etc. due to lower frequency of changing heaters. |
Shorter usage life for barrel, screw etc. |
Environment | Lower environment temperature; No noise | Much higher environment temperature and much noise |
Induction Heating Power Calculation
In the case of knowing the heating power of existing heating system, selecting an appropriate power according to load rate
- Load rate ≤ 60%, applicable power is 80% of the original power;
- Load rate between 60%-80%, select the original power;
- Load rate > 80%, applicable power is 120% of the original power;
When the heating power of existing heating system is unknown
- For injection molding machine, blown film machine and extrusion machine, the power should be calculated as 3W per cm2 according to the actual surface area of the cylinder (barrel);
- For dry cut pelletizing machine, the power should be calculated as 4W per cm2 according to the actual surface area of the cylinder (barrel);
- For wet cut pelletizing machine, the power should be calculated as 8W per cm2 according to the actual surface area of the cylinder (barrel);
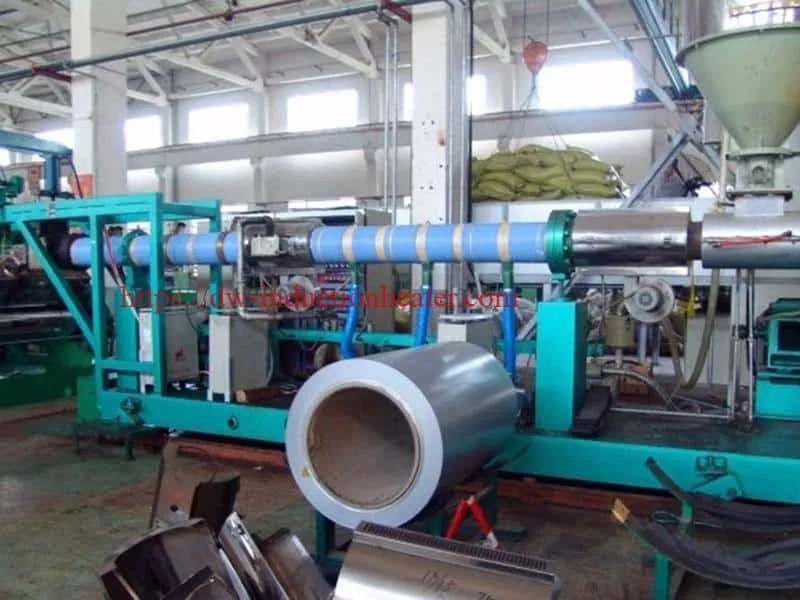