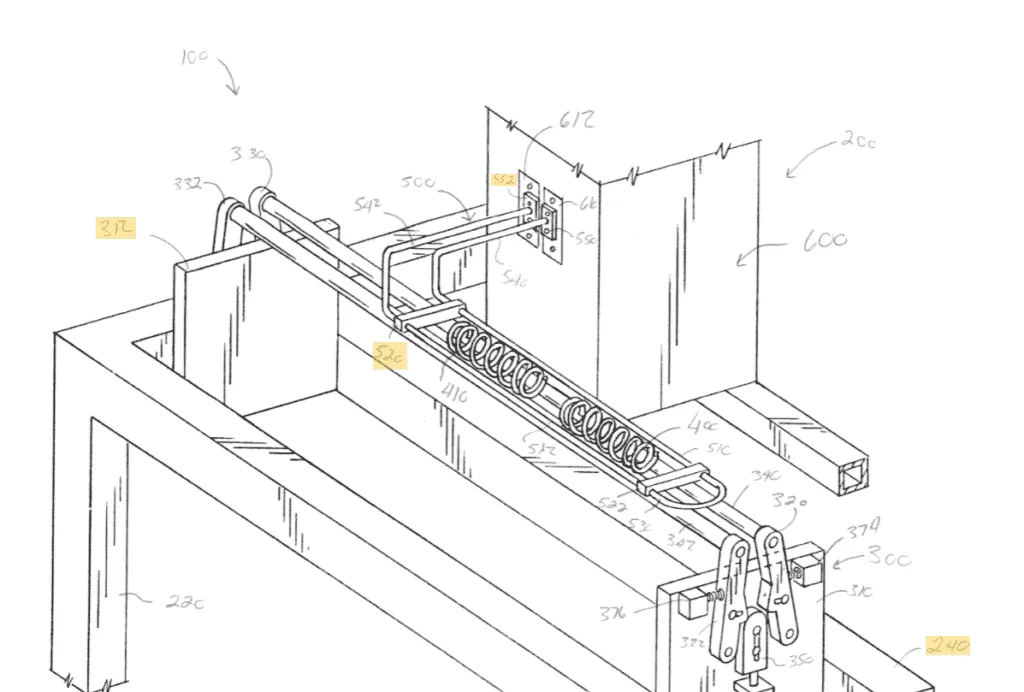


Technical Parameters:
Model |
DW-MF-70KW |
|
Input power desire |
3 phase,380V±10%, 50/60HZ |
|
Oscillate power max |
70KW |
|
Max input current |
105A |
|
Oscillate frequency |
1-20KHz |
|
Cooling water desire |
>0.2MPa 6L/Min |
|
Duty cycle |
100% ,40°C |
|
Dimensions |
Generator |
560*270*470mm |
Transformer |
550*300*420mm |
|
Net weight |
45kg/55kg |
|
Cable length |
2-6(Meters) |
Spare Parts For DW-MF-70KW
Item |
Name of machine or parts |
Specification |
Amount |
1 |
DW-MF-70KW Generator |
- |
1 pc |
2 |
DW-MF-70KW transformer |
- |
1 pc |
3 |
Foot switch |
- |
1 pc |
4 |
Induction Coils |
- |
2 sets |
5 |
Coil connect pole |
- |
2 set |
6 |
Instruction Manual |
- |
1 |
7 |
Packing list and receipt |
- |
1 |
8 |
Guarantee card |
- |
1 |
9 |
Products certificate |
- |
1 |
Steamers in current use, such as cooking steamers, convection ovens, cooking steam warmers, steamers for defrosting frozen food, steamers for processing tea leaves, steam baths for household use, steamers for cleaning, and steamers used in restaurants and hotels, are widely used as equipment for utilizing the steam they generate.Generally, fossil fuels (gas, petroleum, crude petroleum, coal and so forth) are burned as heat sources for large steamers in current use. This heating method, however, is not economical for compact steamers.
Relatively compact steamers in current use commonly employ electrical resistance heaters as a heat source. Such steamers obtain steam intermittently by spraying water on an iron plate which has been heated in advance with a heater or the heater's protecting tube from inside or beneath the plate.
Item content / model | Rated power (KW) | Rated steam temperature (℃) | Rated current (A) | Rated steam pressure (mpa) | Evaporation (kg/h) | Thermal efficiency (%) | Input voltage (V/HZ) | Cross section of input power cord (MM2) | Steam outlet diameter | Relief valve diameter | Inlet diameter | Drainage diameter | Overall dimensions (mm) |
HLQ-10 | 10 | 165 | 15 | 0.7 | 14 | 97 | 380/50HZ | 2.5 | DN20 | DN20 | DN15 | DN15 | 450*750*1000 |
HLQ-20 | 20 | 165 | 30 | 0.7 | 28 | 97 | 380/50HZ | 6 | DN20 | DN20 | DN15 | DN15 | 450*750*1000 |
HLQ-30 | 30 | 165 | 45 | 0.7 | 40 | 97 | 380/50HZ | 10 | DN20 | DN20 | DN15 | DN15 | 650*950*1200 |
HLQ-40 | 40 | 165 | 60 | 0.7 | 55 | 97 | 380/50HZ | 16 | DN20 | DN20 | DN15 | DN15 | 780*950*1470 |
HLQ-50 | 50 | 165 | 75 | 0.7 | 70 | 97 | 380/50HZ | 25 | DN20 | DN20 | DN15 | DN15 | 780*950*1470 |
HLQ-60 | 60 | 165 | 90 | 0.7 | 85 | 97 | 380/50HZ | 25 | DN20 | DN20 | DN15 | DN15 | 780*950*1470 |
HLQ-80 | 80 | 165 | 120 | 0.7 | 110 | 97 | 380/50HZ | 35 | DN25 | DN20 | DN15 | DN15 | 680*1020*1780 |
HLQ-100 | 100 | 165 | 150 | 0.7 | 140 | 97 | 380/50HZ | 50 | DN25 | DN20 | DN25 | DN15 | 1150*1000*1730 |
HLQ-120 | 120 | 165 | 180 | 0.7 | 165 | 97 | 380/50HZ | 70 | DN25 | DN20 | DN25 | DN15 | 1150*1000*1730 |
HLQ-160 | 160 | 165 | 240 | 0.7 | 220 | 97 | 380/50HZ | 95 | DN25 | DN20 | DN25 | DN15 | 1150*1000*1880 |
HLQ-240 | 240 | 165 | 360 | 0.7 | 330 | 97 | 380/50HZ | 185 | DN40 | DN20 | DN40 | DN15 | 1470*940*2130 |
HLQ-320 | 320 | 165 | 480 | 0.7 | 450 | 97 | 380/50HZ | 300 | DN50 | DN20 | DN50 | DN15 | 1470*940*2130 |
HLQ-360 | 360 | 165 | 540 | 0.7 | 500 | 97 | 380/50HZ | 400 | DN50 | DN20 | DN50 | DN15 | 2500*940*2130 |
HLQ-480 | 480 | 165 | 720 | 0.7 | 670 | 97 | 380/50HZ | 600 | DN50 | DN20 | DN50 | DN15 | 3150*950*2130 |
HLQ-640 | 640 | 165 | 960 | 0.7 | 900 | 97 | 380/50HZ | 800 | DN50 | DN20 | DN50 | DN15 | 2500*950*2130 |
HLQ-720 | 720 | 165 | 1080 | 0.7 | 1000 | 97 | 380/50HZ | 900 | DN50 | DN20 | DN50 | DN15 | 3150*950*2130 |
Model |
DW-HF-25KW-B(A) |
|
Input power desire |
3*380 380V 50-60HZ |
|
Oscillate power max |
25KVA |
|
Duty cycle |
100%30°C |
|
Cubage |
Host computer |
550x240x485mm |
Extension |
340x205x340mm |
|
Weight |
55kg |
|
Cable length |
2m |
|
Oscillate frequency |
30-80KHz |
Type | Input Power | Melting Capacity | Max Temperature | ||
steel, stainless steel | copper, gold, silver (scrap, Slag) | aluminum, aluminum alloy, Aluminum scrap, Aluminum slag, pop can | 1800℃ | ||
SMJD-463 | 60 KW | 200 KG | 500 KG | 200 KG | |
SMJD-480 | 60 KW | 150 KG | 500 KG | 150 KG | |
SMJD-580 | 80 KW | 200 KG | 600 KG | 200 KG | |
SMJD-600 | 60 KW | 230 KG | 560 KG | 230 KG | |
SMJD-900 | 120 KW | 300 KG | 900 KG | 300 KG | |
SMJD-905 | 80 KW | 300 KG | 900 KG | 300 KG | |
SMJD-1250 | 80 KW | 400 KG | 1200 KG | 400 KG | |
SMJD-1250 | 120 KW | 450 KG | 1350 KG | 450 KG | |
SMJD-1500 | 120 KW | 500 KG | 1500 KG | 500 KG | |
SMJD-1550 | 120 KW | 520 KG | 1560 KG | 520 KG | |
SMJD-1700 | 160KW | 600 KG | 1700 KG | 600 KG | |
SMJD-2300 | 160KW | 800 KG | 2000 KG | 800 KG | |
SMJD-3100 | 200KW | 1200 KG | 3000 KG | 1200 KG |
MF Series Electric Mini Gold Melting Furnace MF series apply SSR controller, alloy made heating element which has melting point up to 1900°C ,high temp proof ceramic melting chamber , high aluminium protection and other advanced, top quality components , in addition to unique design, all consolidate furnace's durability and working efficiency over current markets furnaces. Max temp of machine:1150°C
Casing Color: Black, red
Instructions
1.will melt gold machine put smoothly 2.and carefully examine whether products,then will cover intact,dissolve gold open check whether the vessel intact 3.connecting swith power supply,electrictity,light switch 4.and the normal work,intelligent temperature controller with the digital furnace temperature and slowly rising,if there are any complicatios,be sure to stop using it 5.in the process of operation,the furnace temperaturedegrees will spread,staff shall not move and collision,avoid scald and damage 6. in june,when the temperature reached gold and gold rains melring point,staff according to demand will continue to increase.when the maximum temperature reached 1,100 degrees in 28°C,will stop work or in cooling condition 7 gold,be sure to disconnect the power supply,then use to operate,go profssional pliers to ensure their safety 8 and shall immediately take gold after moving machines,owing to the high temperature,can easily damaged internal components,and burns itself to its cooling,10-20 minutes,to ensure the service life of the products 9 every time interval must be in 30-60 minutes,very easy to damage the product 10 for precision machine,plz dont remove the professional technology,to ensure accuracy 11 plz pay attention to safety and maintain normal use of electric mini gold melting furnace