Induction quenching is a surface hardening process that involves heating a metal component using induction heating and then rapidly cooling it to achieve a hardened surface. This process is widely used in various industries, including automotive, aerospace, and manufacturing, to improve the wear resistance and durability of metal components. In this article, we will explore the applications of induction quenching surface treatment and its benefits in different industries.
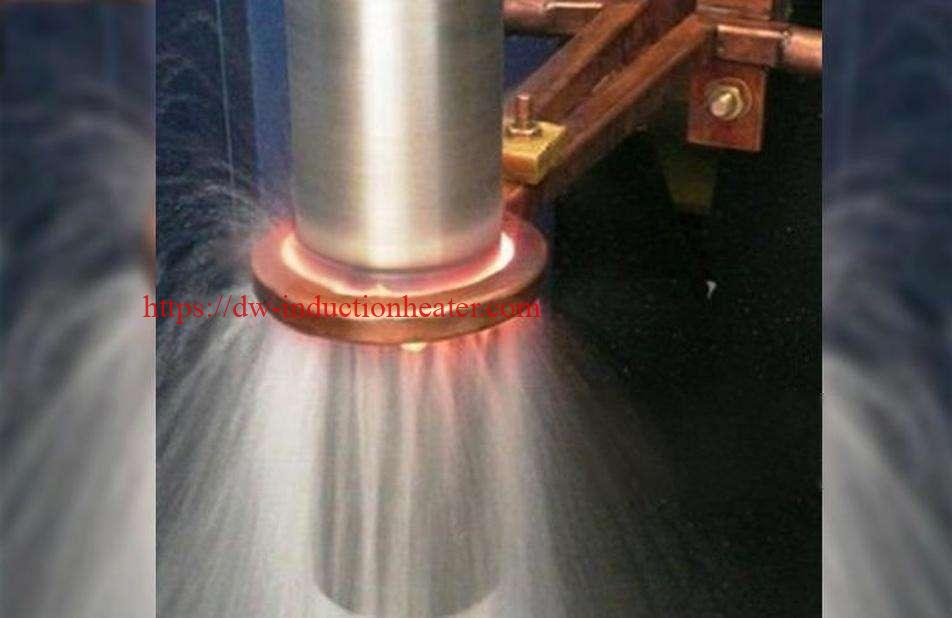
Automotive Industry:
The automotive industry is one of the largest users of induction quenching for surface hardening applications. Components such as gears, shafts, and camshafts are often subjected to induction quenching to improve their wear resistance and fatigue strength. Induction quenching allows for precise control over the hardening depth and pattern, making it an ideal choice for automotive components that require high precision and consistency.
Aerospace Industry:
In the aerospace industry, induction quenching is used to improve the performance and longevity of critical components such as landing gear parts, turbine blades, and engine components. These parts are often subjected to extreme conditions during operation, and induction quenching helps to increase their resistance to wear, corrosion, and fatigue. The ability to selectively harden specific areas of a component makes induction quenching an attractive option for aerospace applications where weight reduction and performance optimization are critical.

Manufacturing Industry:
In the manufacturing industry, induction quenching is used for a wide range of applications, including tooling, dies, molds, and machine components. These components are often subjected to high levels of wear and abrasion during operation, making them ideal candidates for induction quenching. By increasing the hardness and wear resistance of these components' surfaces through induction quenching, manufacturers can extend their service life and reduce downtime due to premature failure.
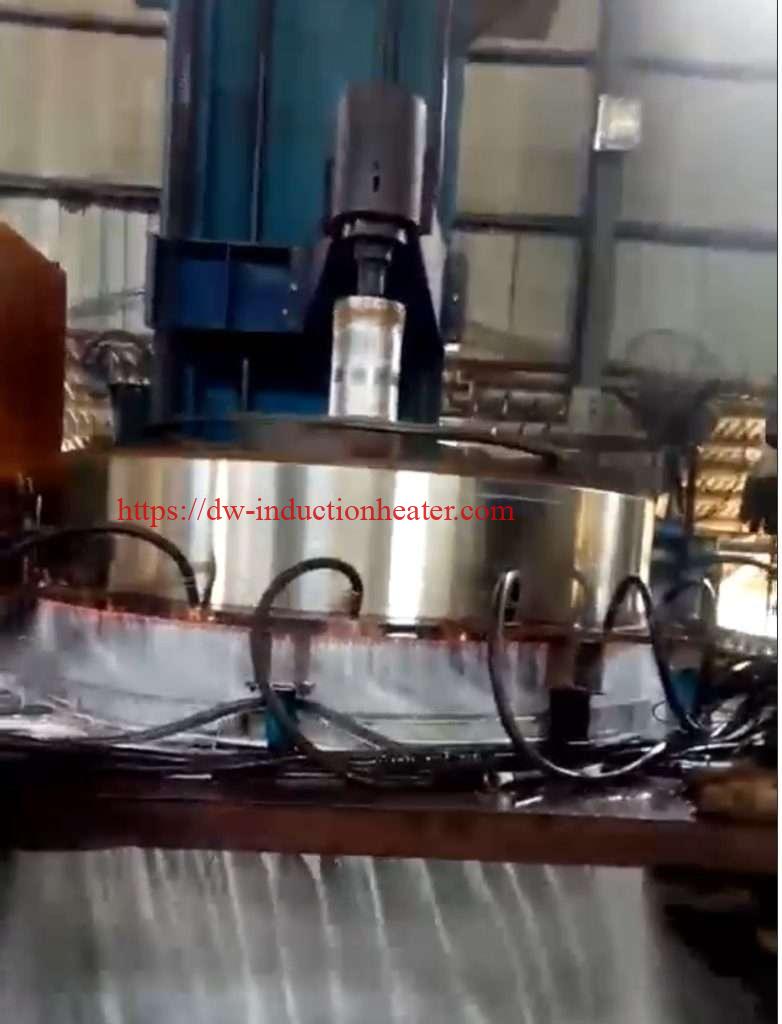
Benefits of
Induction Quenching Surface Treatment:
1. Improved Wear Resistance: Induction quenching significantly increases the hardness of a metal component's surface layer, making it more resistant to wear from frictional forces.
2. Enhanced Fatigue Strength: Components that undergo induction quenching exhibit improved fatigue strength due to the transformation of their microstructure into a hardened state.
3. Precise Control: Induction quenching allows for precise control over the depth and pattern of hardening on a component's surface, enabling tailored solutions for specific applications.
4. Reduced Distortion: Compared to traditional heat treatment methods such as flame or furnace heating, induction quenching minimizes distortion in metal components due to its localized heating approach.
5. Energy Efficiency: Induction heating is an energy-efficient process that minimizes heat loss compared to other heating methods like flame or furnace heating.
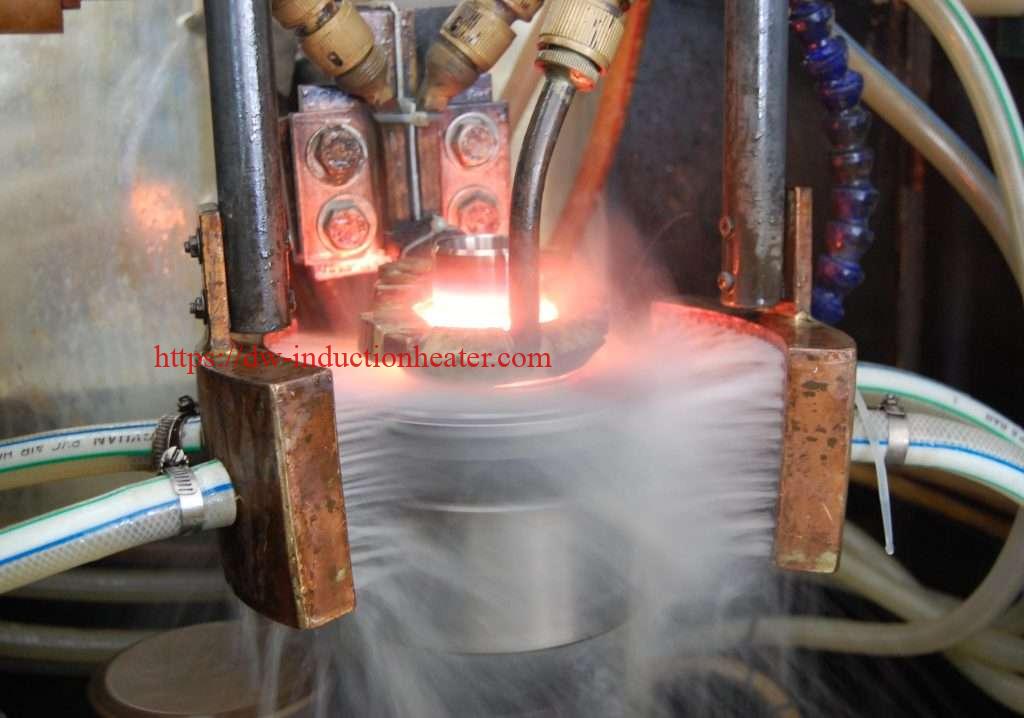
6. Environmentally Friendly: Induction quenching produces minimal emissions or waste products compared to other heat treatment methods that involve combustion processes.
7. Cost-Effective: The precision control offered by induction quenching reduces material waste by minimizing over-treatment or rework requirements.
Conclusion:
Induction quenching surface treatment offers numerous benefits across various industries by improving the wear resistance and durability of metal components while maintaining tight tolerances on critical dimensions. Its ability to selectively harden specific areas makes it an attractive option for applications where precision control is essential. As technology continues to advance in this field with improvements in equipment design and process optimization techniques, we can expect further advancements in induction quenching's capabilities across different industries in the future.
https://dw-inductionheater.com/induction-quenching-surface-applications.html?feed_id=231259&_unique_id=6580f9d493705