The Benefits of Induction Brazing Copper Plates and copper busbars for Your Business
Induction brazing copper plates and busbars is a process that involves joining two or more copper plates using a filler metal that has a lower melting point. Induction brazing is a highly efficient and cost-effective way of joining copper plates, as it uses electromagnetic induction to heat the copper plates and the filler metal to their melting point. In this article, we will explore the benefits, applications, and process of induction brazing copper plates.
Benefits of Induction Brazing Copper Plates:
1. High Strength Joints: Induction brazing copper plates produces high-strength joints that are capable of withstanding high temperatures, pressures, and vibrations. This makes it an ideal choice for applications that require high mechanical strength.
2. Cost-Effective: Induction brazing copper plates is a highly efficient and cost-effective way of joining copper plates. It uses electromagnetic induction to heat the copper plates and the filler metal, which reduces the time and energy required for the process.
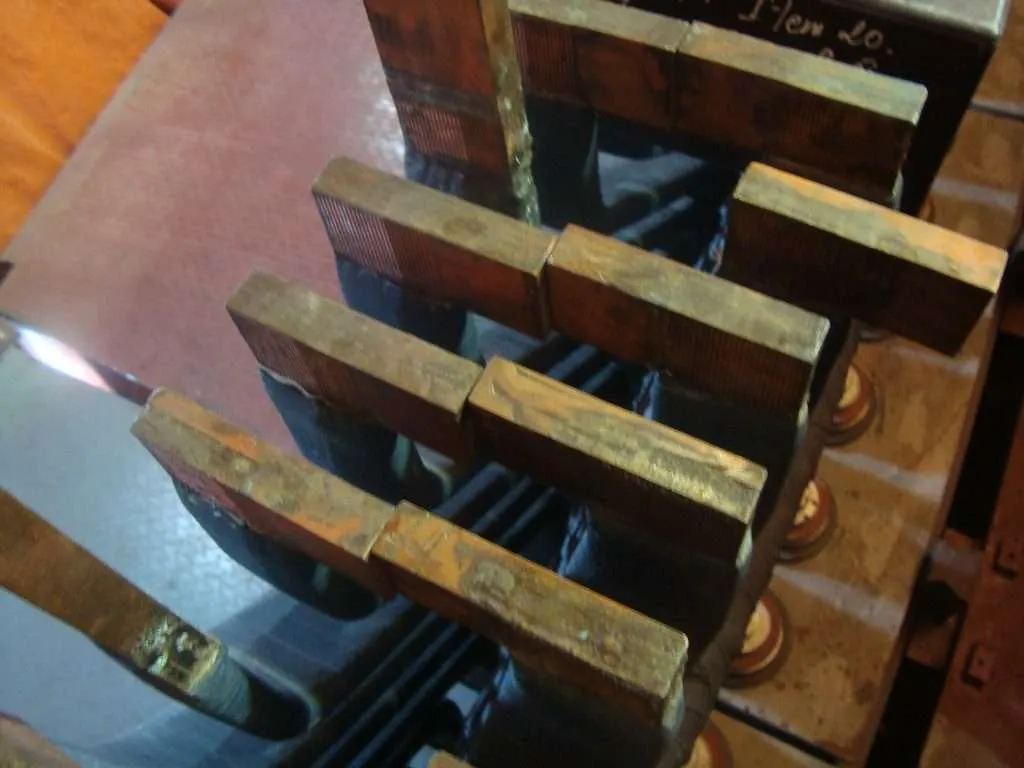
3. Precise Control: Induction brazing copper plates offers precise control over the heating process, which allows for consistent and repeatable results. This is especially important for applications that require high precision and accuracy.
4. Clean Process: Induction brazing copper plates is a clean process that does not require any flux or chemicals. This results in a clean and environmentally friendly process.
Applications of Induction Brazing Copper Plates:
1. Heat Exchangers: Induction brazing copper plates is commonly used in the manufacturing of heat exchangers. Copper plates are brazed together to form a stack, which is then used to transfer heat between two fluids.
2. Electrical Conductors: Induction brazing copper plates is also used in the manufacturing of electrical conductors. Copper plates are brazed together to form a conductor, which is then used to transmit electrical currents.

3. Automotive Industry:
Induction brazing copper plates is used in the manufacturing of automotive radiators, oil coolers, and air conditioning systems. Copper plates are brazed together to form a heat exchanger, which is then used to transfer heat between fluids.
4. Aerospace Industry: Induction brazing copper plates is used in the manufacturing of aerospace heat exchangers, which are used to regulate the temperature of aircraft engines. Copper plates are brazed together to form a heat exchanger, which is then used to transfer heat between fluids.
Process of Induction Brazing Copper Plates:
1. Preparation: The first step in induction brazing copper plates is to prepare the copper plates and the filler metal. The copper plates must be cleaned and degreased, and the filler metal must be cut to the required size.
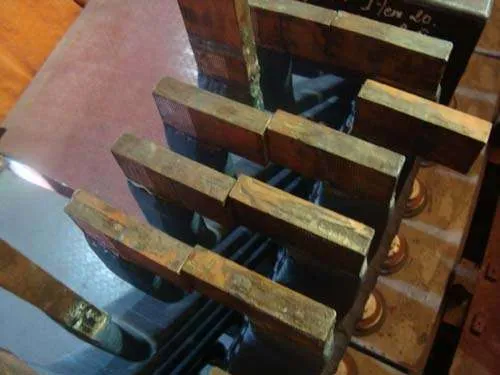
2. Assembly: The copper plates and the filler metal are then assembled in a jig or fixture. The jig or fixture holds the copper plates and the filler metal in the correct position for brazing.
3. Heating: The assembly is then placed in an induction heating coil, which generates an electromagnetic field that heats the copper plates and the filler metal to their melting point. The filler metal melts and flows into the joint between the copper plates, creating a bond.
4. Cooling: The assembly is then allowed to cool naturally or is quenched in water or oil. The cooling process solidifies the filler metal, creating a strong bond between the copper plates.
Advantages of Induction Brazing Copper Plates:
1. High Productivity: Induction brazing copper plates is a highly productive process that can join multiple copper plates simultaneously. This results in a high production rate, which reduces the time and cost required for the process.
2. Reduced Energy Consumption: Induction brazing copper plates uses electromagnetic induction to heat the copper plates and the filler metal, which reduces the energy consumption of the process. This results in lower operating costs and a more environmentally friendly process.
3. Consistent Quality: Induction brazing copper plates offers consistent and repeatable results, which ensures the quality of the finished product. This is especially important for applications that require high precision and accuracy.
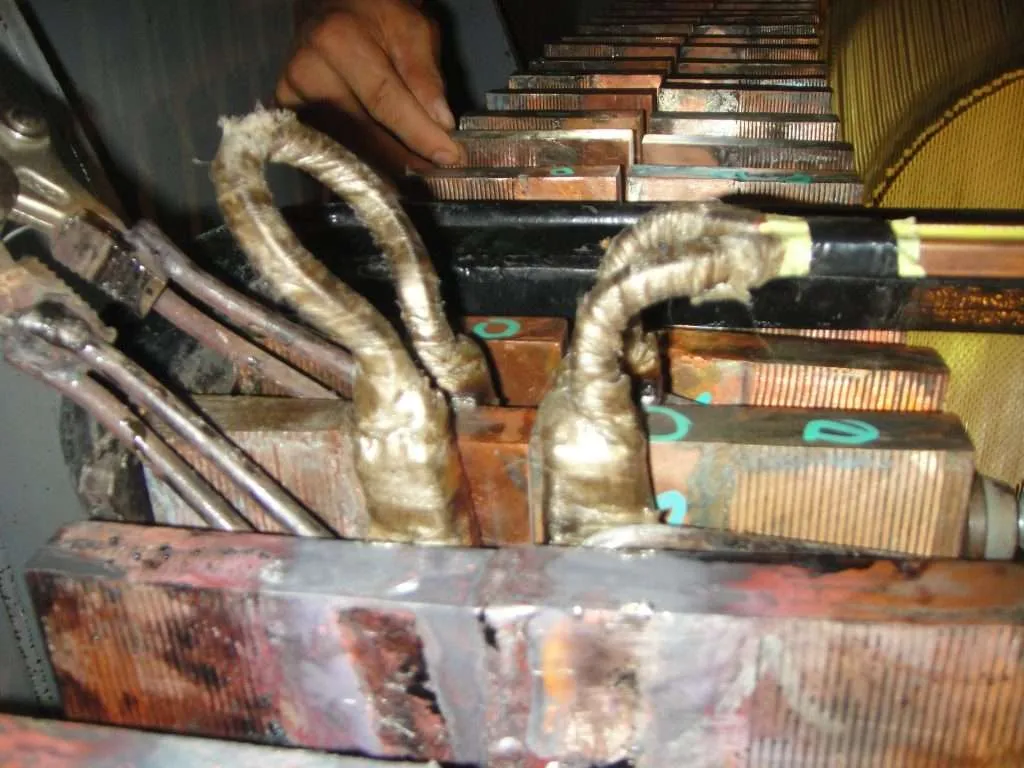
4. Reduced Material Waste: Induction brazing copper plates produces a minimal amount of material waste, which reduces the cost and environmental impact of the process.
5. Safe Process: Induction brazing copper plates is a safe process that does not require any open flames or hazardous chemicals. This results in a safer working environment for operators and reduces the risk of accidents.
Challenges of Induction Brazing Copper Plates:
1. Equipment Cost: Induction brazing copper plates requires specialized equipment, which can be expensive to purchase and maintain. This can be a barrier to entry for small businesses or those with limited budgets.
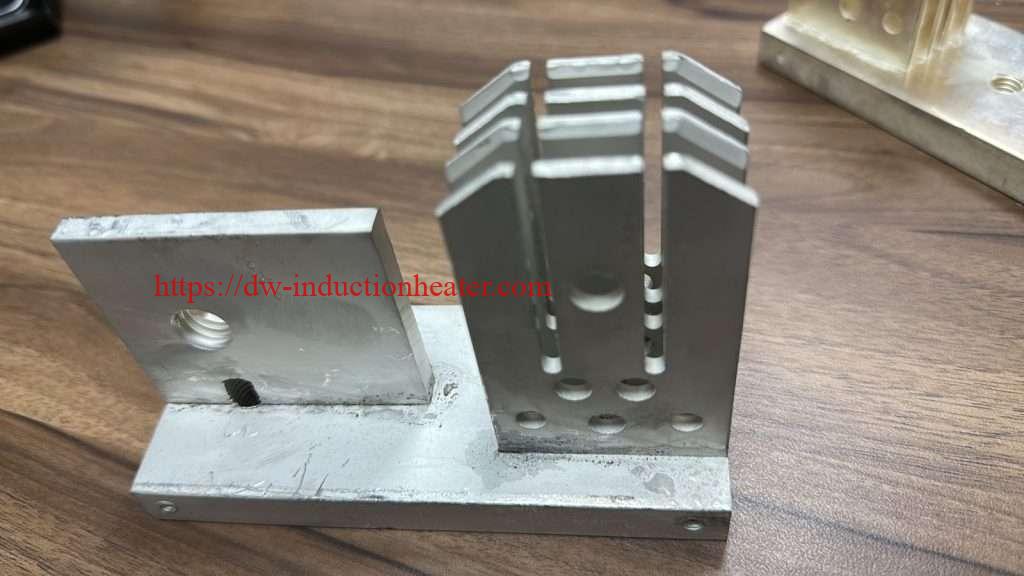
2. Material Compatibility: Not all copper alloys are compatible with
induction brazing, which can limit the range of applications for the process.
3. Joint Strength: The joint strength of induction brazed copper plates can be affected by the quality of the filler metal and the brazing process. This can result in weaker joints that are not suitable for certain applications.
4. Process Control: Induction brazing copper plates requires precise control over the heating process, which can be challenging to achieve. Any variation in the heating process can affect the quality of the finished product.
Conclusion:
Induction brazing copper plates and busbars is a highly efficient and cost-effective way of joining copper plates. It offers high-strength joints, precise control, and a clean process.

Induction brazing copper plates is used in a wide range of applications, including heat exchangers, electrical conductors, and the aerospace andautomotive industries. The process of induction brazing copper plates involves preparation, assembly, heating, and cooling. With its many benefits and applications, induction brazing copper plates is a valuable addition to any manufacturing process. However, it also presents challenges such as equipment cost, material compatibility, joint strength, and process control. By understanding these challenges and implementing best practices, manufacturers can optimize the
induction brazing process for their specific applications and achieve high-quality results.
https://dw-inductionheater.com/the-benefits-of-induction-brazing-copper-plates-and-copper-busbars-for-your-business.html?feed_id=215531&_unique_id=64955e6fb8802