Induction brazing copper busbars is a process that involves the joining of two or more copper busbars using a heated filler metal. This process is used extensively in industries such as electrical, automotive, and aerospace industries. Copper busbars are commonly used in these industries because of their high conductivity, thermal stability, and corrosion resistance.
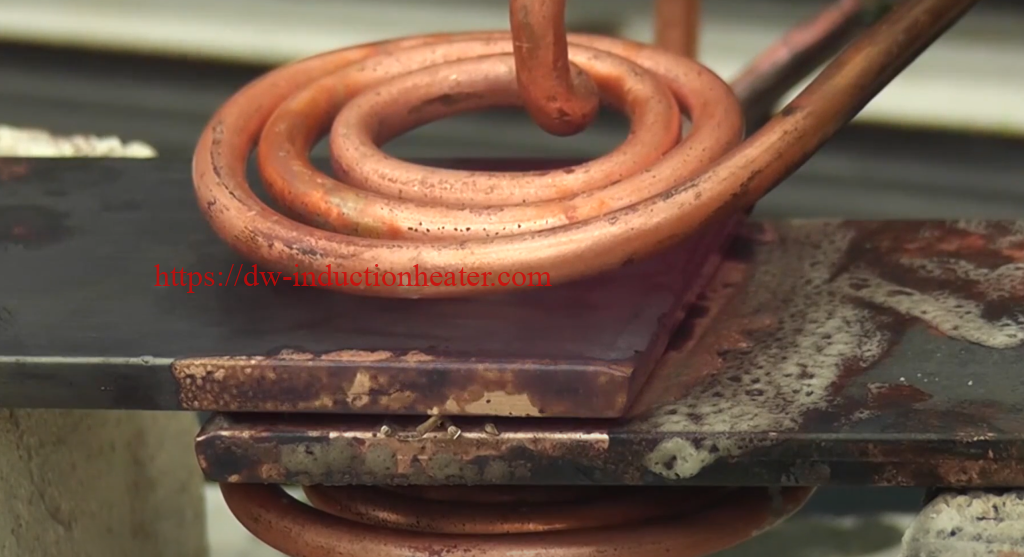
Induction brazing is a process that uses an induction coil to generate heat in the copper busbars and the filler metal. The heat generated is used to melt the filler metal, which is then used to join the copper busbars. This process is fast, efficient, and produces high-quality brazed joints.
In this article, we will discuss the process of induction brazing copper busbars in detail. We will cover the equipment required, the brazing process, the advantages of induction brazing, and the applications of induction brazing copper busbars.
Equipment Required for Induction Brazing Copper Busbars
The equipment required for induction brazing copper busbars includes an induction brazing machine, an induction coil, a power source, a filler metal, and a flux.
Induction brazing machines are available in different sizes and configurations. These machines generate a high-frequency magnetic field that induces an electric current in the copper busbars and the filler metal. This current generates heat in the material, which is used to melt the filler metal and join the copper busbars.
The
induction coil is a critical component of the induction brazing machine. The coil is designed to generate a high-frequency magnetic field that induces an electric current in the copper busbars and the filler metal. The shape and size of the coil determine the distribution of the magnetic field and the heat generated.
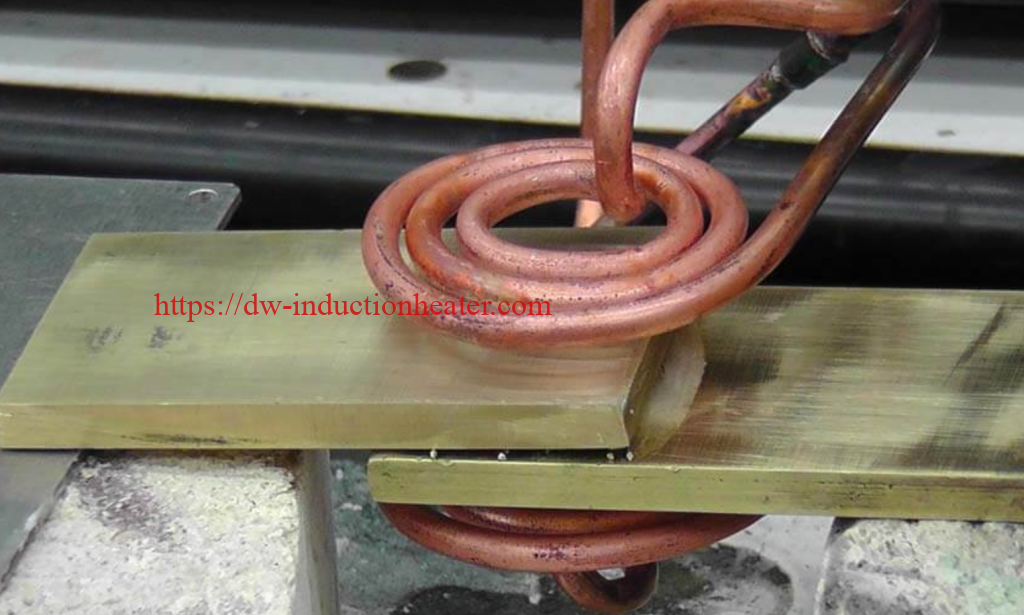
The power source is used to supply the induction brazing machine with the required electrical power. The power source is typically a high-frequency power supply that is designed to deliver a stable and consistent output.
The filler metal is the material used to join the copper busbars. The filler metal is typically a silver-based alloy that has a melting point lower than that of the copper busbars. The filler metal is available in different forms, such as rods, wires, and powders.
The flux is a material used to clean the surfaces of the copper busbars and the filler metal. The flux removes any oxide layers that may be present on the surfaces and promotes wetting of the solder. The flux also helps to reduce the formation of voids and defects in the brazed joint.
Induction Brazing Process
The induction brazing process involves several steps. These steps include surface preparation, flux application, filler metal placement, and induction brazing.
Surface Preparation
Surface preparation is a critical step in the induction brazing process. The surfaces of the copper busbars and the filler metal must be clean and free of any contaminants such as oils, grease, and oxide layers. This is because any contaminants on the surfaces can affect the quality of the brazed joint.
The surfaces of the copper busbars and the filler metal can be cleaned using a variety of methods such as mechanical cleaning, chemical cleaning, or abrasive blasting. Mechanical cleaning involves using abrasives such as sandpaper or wire brushes to remove any contaminants from the surfaces. Chemical cleaning involves using solvents or acids to remove any contaminants from the surfaces. Abrasive blasting involves using compressed air to propel abrasive particles onto the surfaces to remove any contaminants.
Flux Application
Once the surfaces are clean, the flux is applied to the surfaces of the copper busbars and the filler metal. The flux helps to remove any remaining oxide layers on the surfaces and promotes wetting of the filler metal.
The flux is typically applied to the surfaces of the copper busbars and the filler metal using a brush or spray applicator. The flux is allowed to dry before the filler metal is placed on the surfaces.
Filler Metal Placement
The filler metal is then placed on the surfaces of the copper busbars. The filler metal can be in the form of wires, rods, or powders. The filler metal is placed on the surfaces using a variety of methods such as hand placement or automated placement.
Induction Brazing
Once the filler metal is in place, the copper busbars and the filler metal are heated using the induction brazing machine. The induction coil generates a high-frequency magnetic field that induces an electric current in the copper busbars and the filler metal. This current generates heat in the material, which is used to melt the filler metal and join the copper busbars.
The induction brazing process is fast, efficient, and produces high-quality brazed joints. The process is also environmentally friendly because it does not produce any harmful emissions.
Advantages of Induction Brazing Copper Busbars
Induction brazing copper busbars offers several advantages over other brazing methods. These advantages include:
1. Fast and Efficient - Induction brazing is a fast and efficient process that can join multiple copper busbars in a short amount of time. This process is ideal for high-volume production.
2. High Quality - Induction brazing produces high-quality brazed joints that are strong, durable, and resistant to corrosion.
3. Precise Control - Induction brazing allows for precise control of the heating process, which helps to ensure consistent brazed joints.
4. Environmentally Friendly - Induction brazing is an environmentally friendly process because it does not produce any harmful emissions.
Applications of Induction Brazing Copper Busbars
Induction brazing copper busbars is used extensively in industries such as electrical, automotive, and aerospace industries. Copper busbars are commonly used in these industries because of their high conductivity, thermal stability, and corrosion resistance.
Induction brazing copper busbars is used in applications such as:
1. Electrical Equipment - Copper busbars are used extensively in electrical equipment such as transformers, switchgear, and power distribution systems.
2. Automotive Industry - Copper busbars are used in automotive applications such as battery packs, charging systems, and electric motors.
3. Aerospace Industry - Copper busbars are used in aerospace applications such as satellites, communication systems, and avionics.
Conclusion
Induction brazing copper busbars is a fast, efficient, and environmentally friendly process that produces high-quality brazed joints. This process is used extensively in industries such as electrical, automotive, and aerospace industries. Copper busbars are commonly used in these industries because of their high conductivity, thermal stability, and corrosion resistance.
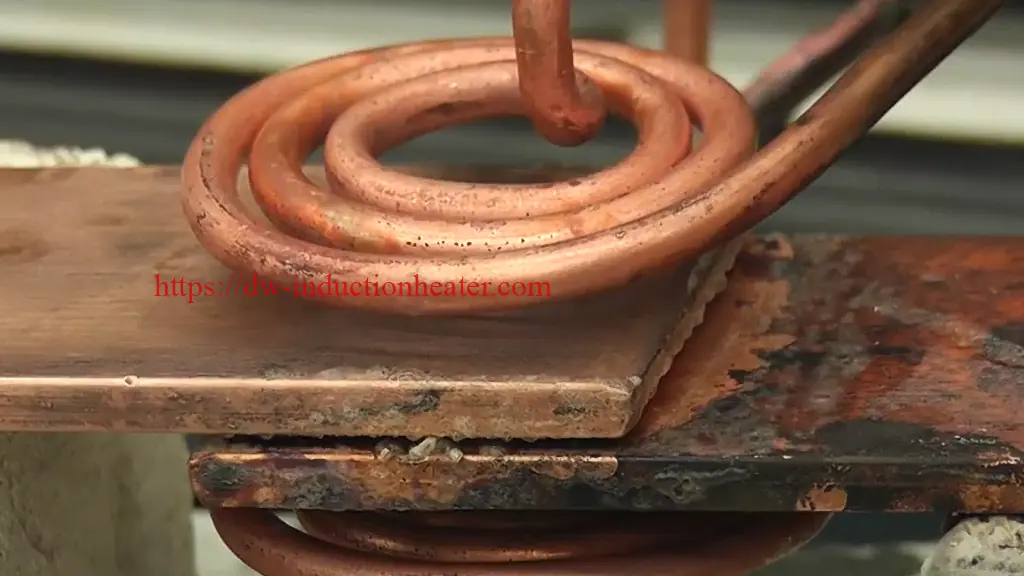
The equipment required for induction brazing copper busbars includes an induction brazing machine, an induction coil, a power source, a filler metal, and a flux. The induction brazing process involves several steps, including surface preparation, flux application, filler metal placement, and induction brazing.
Induction brazing copper busbars offers several advantages over other brazing methods. These advantages include fast and efficient, high quality, precise control, and environmentally friendly.
Overall, induction brazing copper busbars is an effective and reliable method for joining copper busbars in a variety of applications.
https://dw-inductionheater.com/induction-brazing-copper-busbars-heating-machine.html?feed_id=215836&_unique_id=6497025c22f7e