induction coating removal for removing paint
Induction coating removal principle
The induction disbonder works by the principle of induction. Heat is generated in the steel substrate and the bonding is broken. The coating is then removed entirely without disintegrating and completely free from contaminating agents, i.e. blast media.This obviously makes disposal and recycling of waste easier and cheaper. Even inside the pittings and cracks in the surface the coating is disbonded. The HLQ Induction heating works by fast transfer of energy to the steel substrate, as a result securing a controlled heating of the surface and fast removal of most types of coatings.What is induction coating removal?
The HLQ Induction coating removal system is a state-of-the-art induction heating tool that rapidly strips paint and tough, high-build coatings. It is a faster, cleaner and safer way to strip coatings.
What are the benefits?
Induction heating can outperform traditional paint-stripping methods. Abrasive blasting or disk grinding are generally more labour intensive and come with other issues such as the cost of enclosure or containment and collection of blast media, plus the filtration or separation of the coating materials for disposal. In many urban projects these are prime considerations and extremely costly to overcome. Whereas, when coatings are removed by induction, the only waste is the coating itself which in most cases can be swept or even vacuumed like any other workshop waste.
Safer working environment: The controlled, localized heat results in significantly reduced fumes and toxic dust.
Easy clean-up: The coating material mainly peels off in flakes rather than being pulverized.
Noiseless operation: Operators can work in public areas without creating a disturbance.
Mobile: The equipment is rugged and reliable but still light-weight and easy to move around worksites.
Reduced energy consumption: Fast, accurate and repeatable heat delivery makes the coating removal process extremely energy efficient.
Method flexibility: Spot heating, scanning, freehand and semi-automatic.
No limitations: The system can be used at flat surfaces, round contours, inside/outside corners, both sides of substrate, round rivets, etc.
Where is it used?
Induction coating removal is used in many industries, such as ships/marine, buildings, storage tanks, pipelines, bridges and offshore.
induction heating involves using alternating current and an induction coil to generate a powerful electro-magnetic field. When used properly, this field generates heat below a coating on a steel substrate, resulting in the coating de-bonding quickly and easily from the metal surface. At Alliance, we use this process to remove coatings from steel such as:
- Multiple coatings including epoxies, urethanes and others
- Lead paint
- Fire-retardant coatings (PFPs)
- Glued and vulcanized rubber as well as chlorinated rubber
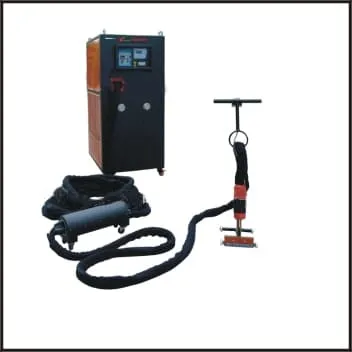
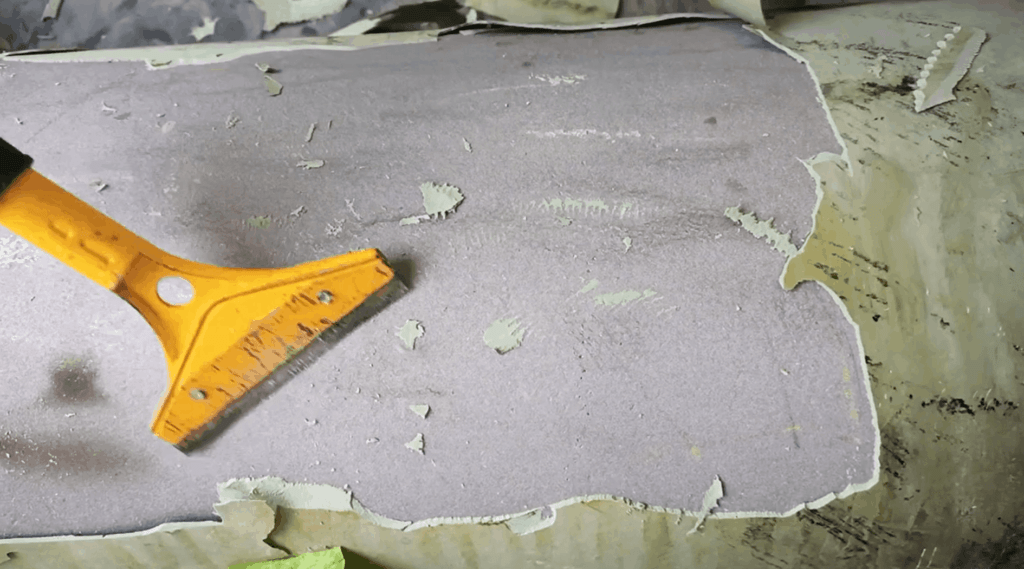
