Iron Steel Melting Furnace|Induction Metal Melting Furnace
Production Description:
1)Medium Frequency Induction Furnace for melting
2)Full digital control system with high accuracy
3) Melting steel, iron,stainless steel,copper,aluminium
4)0.15-20 tons capacity
5)Constant power output, speedy melting, good electricity saving efficiency.
6) Steel shell furnace structure, hydraulic tilting.
3.Usage: Medium Frequency Induction Furnace Mainly used in melting steel, iron, copper, aluminum and alloy, is with high melting efficiency, good electricity saving effect, good metal component uniformity, less burning loss, speedy temperature rise, easy control of temperature, is suitable to all kinds of metal melting.
4.Characters and Advantages:
1) Constant power output, speedy melting, good electricity saving efficiency.
2) Zero-voltage sweep-frequency style start, adapts to requirement of frequently start.
3) Comprehensive protection functions, such as overcurrency protection, overvoltage protection, current-limiting protection, voltage-limiting, water-break protection, and default protection, equipment runs reliably under premise of melting speed guarantee.
4) Easy to operate, suitable for all casting process.
Product-characteristics
-Efficient
Single furnace melting time can be as fast as < 40 minutes! power factor of the furnace is always reached the highest state (≧0.96)!
During the smelting, no matter how the furnace condition changes, the medium frequency power supply always full power output. That is to say, without the operator manual adjustment, the whole process from smelting to the end , the intermediate frequency power supply will always be able to deliver the maximum power to the furnace.
-Energy saving
Extremely competitive energy consumption index (cast iron about 530 kwh/T)! Compared with common parallel inverter power energy saving about 20%.
-Harmonic
Achieve international harmonic current and voltage allowable value!
Using full-wave rectifier power supply series, in the whole working process of the rectifier is always in a state of full open (equivalent to a diode rectifier), do not produce higher harmonic, basic no pollution to power network, does not affect the operation of substation reactive power compensation capacitor.
-Coil
firs-class induction coil design can effectively reduce coil losses.
The induction coil loss of medium frequency furnace accounts for 25% of the total power, so the scientific and rational design of the coil is particularly important. When designing the coil, we adopts the high quality TU1 anoxic copper in aluminum copper, and the coil joint adopts high silver brazing, which has high conductivity and small loss. To Ensure the best spacing of turns, the insulation materials are implanted between turns, the insulation level is improved and the maximum electric thermal efficiency is obtained.
Stable & Environmental Protection
-Stabilization
High standard component selection to ensure the stability of the equipment.
①Imported high pressure carbon-free hose and 304 stainless steel clamp: durable!
②Optical fiber transmission inverter trigger pulse signal plate: strong ability of anti-interference and stable operation
③The high quality special heavy platform Thyristor、square type water cooling radiator(HengYang Patent No. ): use more convenient !
④Customized capacitor: horizontal structure, safer insulation outer shell, using the high strength of the magnesium aluminum alloy, more anti-corrosion and more durable.
⑤Conductive copper bar: Large, thick copper can reduce heat loss and save energy! Copper sandblasted surface and anti-oxidation coating, the contact surface is more conductive, the appearance does not fade and makes more beautiful!
⑥Isolation (exchange) switch : when the furnace is replaced or overhauled, it is possible to control the power failure of one furnace without affecting the normal operation of another furnace. The design of safety and humanization.
⑦Plate heat exchange system (HengYang Patent No. ): to ensure the cooling water temperature in the equipment, and to prevent the external hard water from entering the power . Care to minimize equipment failure.
-Environmental protection
Iron Steel Melting Furnace using whirlwind and side suction heat- preservation furnace cover, dust hood (ring) through a certain air absorb dust, waste gas generated in smelting, reach and improve the effect of exhaust emissions, to meet the requirements of environmental impact assessment design.
Main Type and Technical Parameters:
Power input (50/60HZ) | Power output | A ton cost energy (KWH/T) |
EAF type Electric furnace capacity | Rated power(KW) | Incoming voltage(V) | Incoming line current(A) | Rectifying pulse number | Rectifier transformer capacity(KVA) | DC voltage(V) | Direct current(A) | Medium frequency voltage(V) | Intermediate frequency KHZ | Melting time(Min) | Cast iron | Red copper | Brass | Aluminum |
GW–0.35T | 250 | 380 | 400 | 6 | Three-phase 315 | 500 | 500 | 750 | 1 | 20-45 | 560 | 420 | 390 | 540 |
GW–0.5T | 350 | 380 | 560 | 6 | Three-phase 400 | 500 | 700 | 750 | 0.8 | 30-50 | 550 | 410 | 380 | 530 |
GW–0.75T | 500 | 380 | 800 | 6 | Three-phase 630 | 500 | 1000 | 750 | 0.8 | 40-50 | 550 | 410 | 380 | 530 |
GW–1T | 800 | 380
750 | 1280
656 | 6
6 | Three-phase 1000
Three-phase 1000 | 500
990 | 1600
808 | 750
1480 | 0.7 | 40-50 | 540 | 400 | 370 | 520 |
GW–1.5T | 1000 | 380
750 | 800
820 | 12
6 | Double three-phase 1250
Three-phase 1250 | 500
990 | 1000
1010 | 750
1480 | 0.7 | 40-60 | 530 | 390 | 360 | 510 |
GW–2T | 1400 | 750
750 | 1148
574 | 6
12 | Three-phase 1800
Double three-phase 1800 | 990
990 | 1414
707 | 1480
1480 | 0.5 | 45-60 | 520 | 380 | 350 | 500 |
GW–3T | 2000 | 750 | 820 | 12 | Double three-phase 2500 | 990 | 1010 | 1480 | 0.5 | 50-70 | 510 | 370 | 340 | 490 |
GW–5T | 3000 | 950 | 1140 | 12 | Double three-phase 4000 | 1260 | 1190 | 1900 | 0.3 | 50-80 | 500 | 360 | 330 | 480 |
GW–10T | 6000 | 950 | 2280 | 12 | Double three-phase 8000 | 1260 | 2380 | 1900 | 0.3 | 50-90 | 490 | 350 | 320 | 470 |
GW–15T | 8000 | 950 | 1520 | 24 | Four three-phase 10000 | 1260 | 1590 | 1900 | 0.3 | 50-90 | 480 | 340 | 310 | 460 |
GW–20T | 10000 | 950 | 1900 | 24 | Four three-phase 12500 | 1260 | 1980 | 1900 | 0.25 | 50-90 | 470 | 330 | 300 | 450 |
GW–30T | 15000 | 950 | 2850 | 24 | Four three-phase 20000 | 1260 | 2980 | 1900 | 0.25 | 50-90 | 470 | 330 | 300 | 450 |
In-furnace temperature: Steel 1650℃ Cast iron 1450℃ Red copper 1150℃ Brass 1000℃ Aluminum 700℃ Zinc 400℃ |
※ The capacity of the electric steel melting furnace is based on the density of steel 7.8 (the density of aluminum is 2.7, so the aluminum of equal weight: the matching power is the same, and the capacity needs x 3 times the furnace body)
※ The melting time and tons of power consumption have important relationship with the equipment matching power, raw material shape, raw material density, worker proficiency,
※ In the form above,the “ton power consumption (kwh/T)” is a new series of power consumption, which will consume 15% or more of the power supply in Common parallel IF power supply
※ Equipment configuration: medium frequency power supply, capacitor cabinet, furnace body (steel shell or aluminum shell), hydraulic station (or reducer) tilting system, water cooling cable etc;
※ The Above is the standard product data, can design different power according to the user demand, non-standard product with different melting speed .
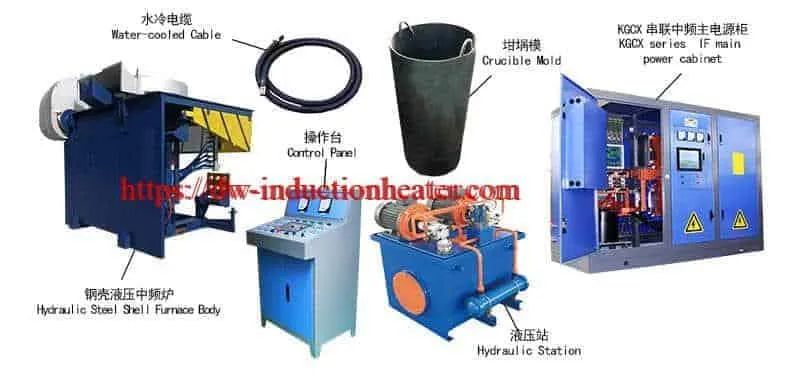
https://dw-inductionheater.com/wp-content/uploads/2019/02/melting-stainless-steel-induction-furnace.jpg
https://dw-inductionheater.com/steel-melting-furnace-induction-metal-melting-furnace.html
buy steel melting furnace, IF steel melting furnace, induction steel melting furnace, iron steel induction furnace, iron steel melting furnace, KGPS steel melting furnace, melting furnace for steel, melting iron steel furnace, melting steel furnace, smelting steel furnace, stainless steel melting furnace, steel induction furnace, steel melting, steel melting furnace, steel melting furnace for sale, steel melting furnace manufacturers, steel scrap melting furnace, steel smelting furnace, steel smelting furnace induction