Huge Gear Hardening Scanner with Induction
Table of contents:
Huge Gear Hardening Scanner with Induction
Introduction to Gear Hardening
The Importance of Gear Hardening
Traditional Gear Hardening Methods
Induction Hardening: A Game-Changer
Precise Control over the Hardening Process
Fast Processing Times
Low Energy Consumption
Minimal Distortion
Additional Benefits of Induction Hardening
Huge Gear Hardening Scanner: The Ultimate Solution
Advanced Technology
Uniform Hardness
Minimal Distortion
Ideal for High-Precision Applications
Customization Options
How the Huge Gear Hardening Scanner Works
- Induction heating:
- Scanning technology:
- Temperature control:
- Cooling system:
Here is the expanded version of the benefits of the Huge Gear Hardening Scanner:
Benefits of the Huge Gear Hardening Scanner
The Huge Gear Hardening Scanner is a cutting-edge technology that offers numerous benefits to gear manufacturers. Some of the key advantages of this system include:
- • Uniform Hardness:
- • Minimal Distortion:
- • Fast Processing Times:
- • Low Energy Consumption:
- Overall
Common Applications of the Huge Gear Hardening Scanner
Aerospace
Automotive
Industrial Machinery
Other Applications
Frequently Asked Questions (FAQS)
- What is gear hardening?:
- What are the benefits of induction hardening?:
- What is the Huge Gear Hardening Scanner?:
- How does the Huge Gear Hardening Scanner work?:
- What are the benefits of the Huge Gear Hardening Scanner?:
- What are the common applications of the Huge Gear Hardening Scanner?:
- Is the Huge Gear Hardening Scanner suitable for small gears?
- Can the Huge Gear Hardening Scanner be customized?
Case Studies
Aerospace:
Automotive:
Industrial machinery:
Conclusion
Glossary
Gear hardening:
Induction hardening:
Scanning technology:
Temperature control:
Cooling system:
Introduction to Gear Hardening
Gear hardening is a critical process in gear manufacturing that involves heating and cooling the gear teeth to achieve the desired level of hardness. The hardness of the gear teeth is essential for ensuring the durability and performance of the gear. Traditional gear hardening methods have been used for decades, but they have limitations. The introduction of induction hardening has revolutionized the gear hardening process, and the Huge Gear Hardening Scanner has taken it to the next level.
The Importance of Gear Hardening
Gear hardening is essential for ensuring the durability and performance of gears. Gears are used in various applications, including automotive, aerospace, and industrial machinery. The hardness of the gear teeth determines the gear's ability to withstand wear and tear, corrosion, and fatigue. Proper gear hardening ensures that the gear teeth are resistant to pitting, cracking, and breaking, which can lead to gear failure.
Traditional Gear Hardening Methods
Traditional gear hardening methods include carburizing, nitriding, and flame hardening. These methods involve heating the gear teeth to a high temperature and then cooling them rapidly to achieve the desired level of hardness. However, these methods have limitations, including:
- Limited control over the hardening process
- Risk of overheating or underheating
- Long processing times
- High energy consumption
Induction Hardening: A Game-Changer
Induction hardening is a non-contact, electromagnetic heating process that uses an induction coil to heat the gear teeth. The induction coil is designed to match the shape of the gear teeth, ensuring uniform heating. Induction hardening offers several advantages over traditional gear hardening methods, including:
Precise Control over the Hardening Process
Induction hardening allows for precise control over the hardening process, which is critical for achieving the desired level of hardness and microstructure. The induction coil is designed to heat the gear teeth uniformly, ensuring that the heat is distributed evenly throughout the tooth. This level of control is not possible with traditional gear hardening methods, which can result in uneven heating and inconsistent hardness.
Fast Processing Times
Induction hardening is a rapid process that can be completed in a matter of seconds or minutes, depending on the size and complexity of the gear. This is significantly faster than traditional gear hardening methods, which can take hours or even days to complete. The fast processing times of induction hardening make it an ideal choice for high-volume production applications.
Low Energy Consumption
Induction hardening is an energy-efficient process that uses significantly less energy than traditional gear hardening methods. The induction coil is designed to heat the gear teeth directly, reducing the amount of energy required to heat the surrounding material. This results in lower energy costs and a reduced environmental impact.
Minimal Distortion
Induction hardening is a non-contact process that does not require the gear to be physically touched or manipulated. This reduces the risk of distortion or damage to the gear, which can occur with traditional gear hardening methods. The minimal distortion of induction hardening makes it an ideal choice for applications where precision and accuracy are critical.
Additional Benefits of Induction Hardening
In addition to the benefits mentioned above, induction hardening also offers several other advantages, including:
- Improved surface finish: Induction hardening can improve the surface finish of the gear teeth, reducing the risk of wear and tear.
- Increased durability: Induction hardening can increase the durability of the gear teeth, reducing the risk of breakage or failure.
- Reduced maintenance: Induction hardening can reduce the maintenance requirements of the gear, as it is less prone to wear and tear.
- Improved performance: Induction hardening can improve the performance of the gear, as it is designed to optimize the microstructure and hardness of the gear teeth.
Overall, induction hardening is a game-changer for gear manufacturing, offering a range of benefits that can improve the performance, durability, and efficiency of gears.
Huge Gear Hardening Scanner: The Ultimate Solution
The Huge Gear Hardening Scanner is a state-of-the-art induction hardening system designed for large gears. The system uses advanced technology to ensure precise control over the hardening process, resulting in uniform hardness and minimal distortion. The Huge Gear Hardening Scanner is ideal for applications where high precision and quality are required.
Advanced Technology
The Huge Gear Hardening Scanner uses advanced technology to ensure precise control over the hardening process. The system is equipped with:
- High-precision temperature control: The system uses advanced temperature control systems to ensure that the gear teeth are heated to the precise temperature required for optimal hardening.
- Advanced scanning technology: The system uses advanced scanning technology to ensure that the gear teeth are heated uniformly, resulting in minimal distortion and uniform hardness.
- Real-time monitoring: The system uses real-time monitoring to ensure that the hardening process is proceeding as planned, allowing for adjustments to be made as needed.
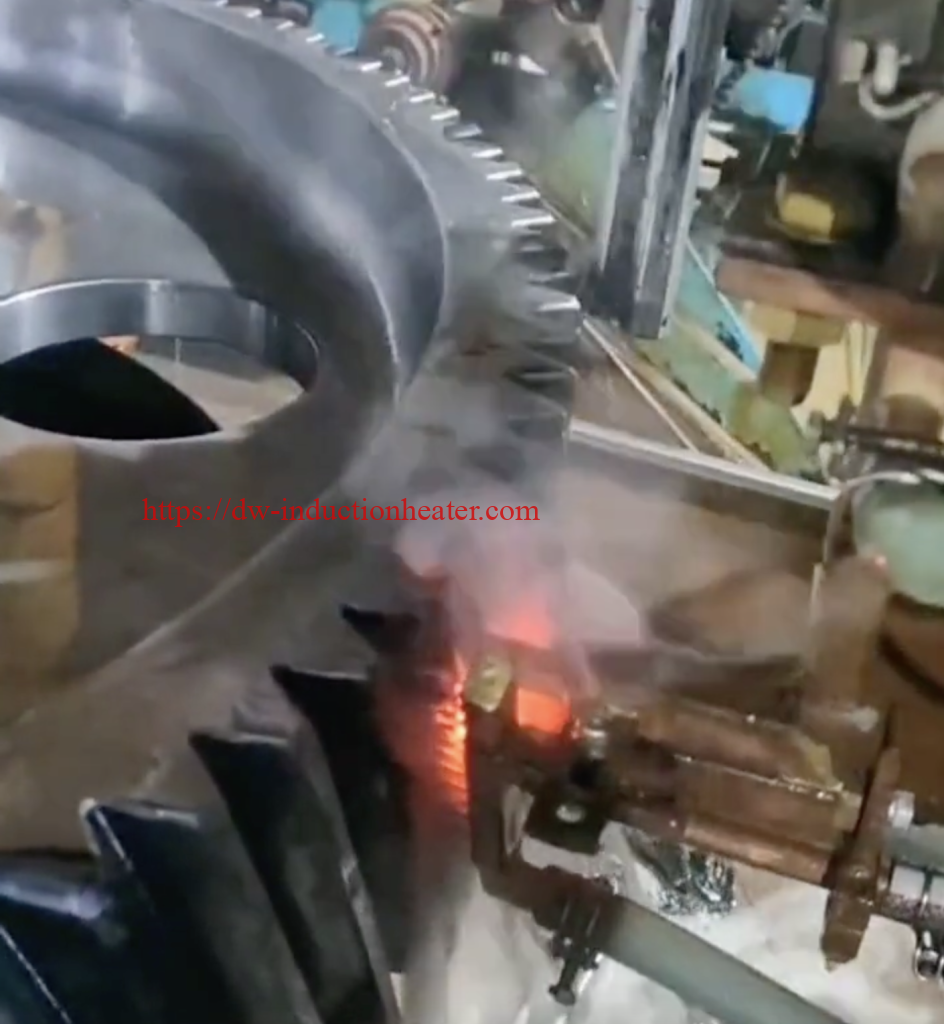
Uniform Hardness
The Huge Gear Hardening Scanner is designed to produce uniform hardness throughout the gear teeth. The system uses advanced technology to ensure that the gear teeth are heated uniformly, resulting in:
- Consistent hardness: The system produces consistent hardness throughout the gear teeth, ensuring that the gear performs optimally.
- Minimal variation: The system minimizes variation in hardness, reducing the risk of gear failure or malfunction.
- Improved durability: The system improves the durability of the gear teeth, reducing the risk of wear and tear.
Minimal Distortion
The Huge Gear Hardening Scanner is designed to minimize distortion during the hardening process. The system uses advanced technology to ensure that the gear teeth are heated uniformly, resulting in:
- Minimal thermal stress: The system minimizes thermal stress, reducing the risk of distortion or cracking.
- Improved dimensional stability: The system improves dimensional stability, ensuring that the gear teeth remain precise and accurate.
- Reduced risk of gear failure: The system reduces the risk of gear failure, ensuring that the gear performs optimally.
Ideal for High-Precision Applications
The Huge Gear Hardening Scanner is ideal for applications where high precision and quality are required. The system is designed for use in a variety of industries, including:
- Aerospace: The system is ideal for use in the aerospace industry, where high precision and quality are critical.
- Automotive: The system is ideal for use in the automotive industry, where high precision and quality are required for optimal performance.
- Industrial machinery: The system is ideal for use in the industrial machinery industry, where high precision and quality are required for optimal performance.
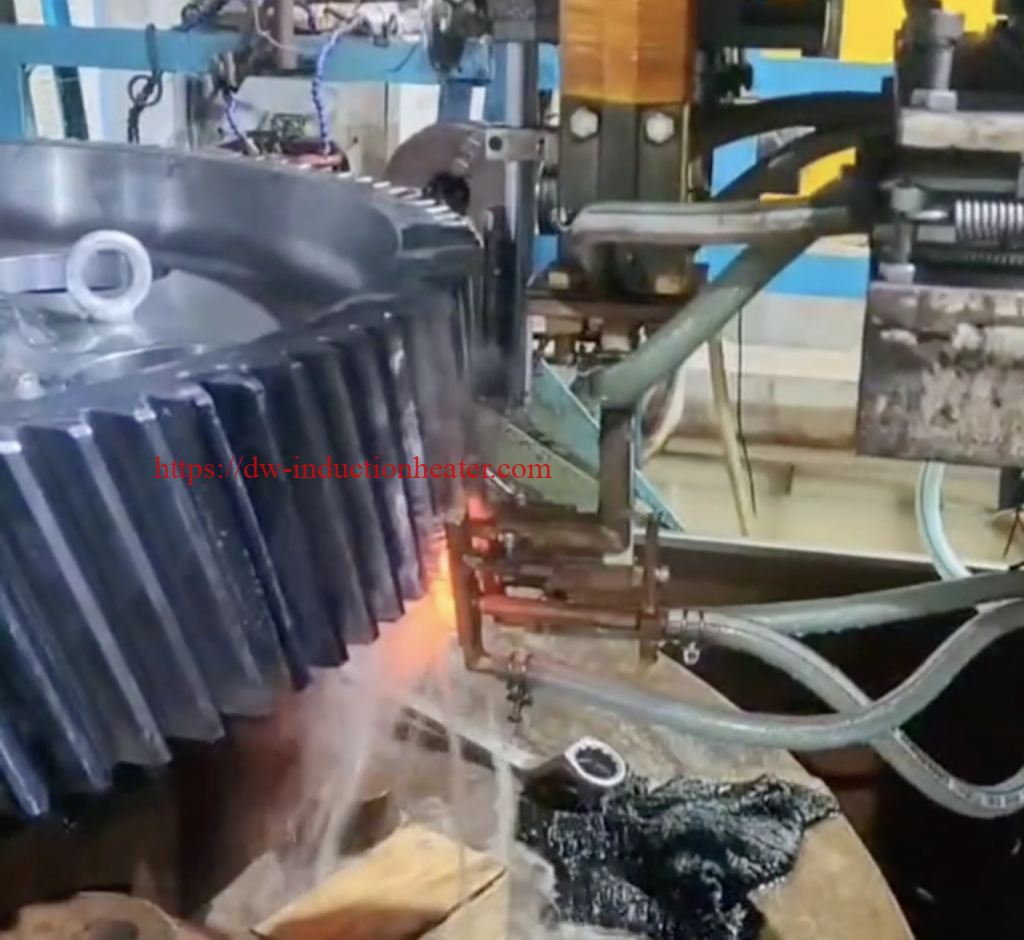
Customization Options
The Huge Gear Hardening Scanner can be customized to meet the specific needs of each application. The system can be configured to accommodate a variety of gear sizes and shapes, and can be integrated with existing production lines. The system can also be customized to meet specific hardness and microstructure requirements.
How the Huge Gear Hardening Scanner Works
The Huge Gear Hardening Scanner uses a combination of advanced technologies, including:
- Induction heating: The system uses an induction coil to heat the gear teeth.
- Scanning technology: The system uses scanning technology to ensure precise control over the hardening process.
- Temperature control: The system uses advanced temperature control systems to ensure uniform heating.
- Cooling system: The system uses a cooling system to rapidly cool the gear teeth.
Here is the expanded version of the benefits of the Huge Gear Hardening Scanner:
Benefits of the Huge Gear Hardening Scanner
The Huge Gear Hardening Scanner is a cutting-edge technology that offers numerous benefits to gear manufacturers. Some of the key advantages of this system include:
- Uniform Hardness: One of the most significant benefits of the Huge Gear Hardening Scanner is its ability to ensure uniform hardness throughout the gear teeth. This is crucial for maintaining the gear's performance and longevity. Uniform hardness helps to prevent uneven wear and tear, reducing the risk of gear failure and improving overall efficiency.
- Minimal Distortion: The system's advanced technology minimizes distortion, ensuring that the gear teeth remain precise and accurate. This is particularly important in high-precision applications, such as aerospace, automotive, and industrial gearboxes, where even slight distortions can lead to costly repairs and downtime.
- Fast Processing Times: The Huge Gear Hardening Scanner offers fast processing times, significantly reducing production time and costs. This is achieved through the system's advanced scanning technology, which quickly and accurately hardens the gear teeth to the required specifications. Faster processing times enable manufacturers to increase productivity, meet tight deadlines, and improve their competitiveness in the market.
- Low Energy Consumption: The system's energy-efficient design reduces energy costs and environmental impact. This is a significant advantage, as manufacturers seek to minimize their carbon footprint and comply with increasingly stringent environmental regulations. By using less energy, the Huge Gear Hardening Scanner helps manufacturers to reduce their operating costs, improve their sustainability, and contribute to a cleaner, healthier environment.
- Overall, the Huge Gear Hardening Scanner offers a range of benefits that can significantly improve gear manufacturing processes. Its ability to ensure uniform hardness, minimize distortion, reduce processing times, and lower energy consumption makes it an attractive solution for manufacturers seeking to improve their productivity, efficiency, and sustainability.
Common Applications of the Huge Gear Hardening Scanner
The Huge Gear Hardening Scanner is ideal for applications where high precision and quality are required, including:
Aerospace
The Huge Gear Hardening Scanner is widely used in the aerospace industry for gear hardening applications. The system is ideal for hardening gears used in aircraft engines, transmission systems, and other critical components. The aerospace industry requires high precision and quality, and the Huge Gear Hardening Scanner delivers.
- Engine gears: The system is used to harden engine gears, which are critical for the performance and safety of aircraft engines.
- Transmission gears: The system is used to harden transmission gears, which are responsible for transmitting power from the engine to the propellers or fans.
- Accessory gears: The system is used to harden accessory gears, which are used to power critical systems such as fuel pumps, oil pumps, and generators.
Automotive
The Huge Gear Hardening Scanner is also widely used in the automotive industry for gear hardening applications. The system is ideal for hardening gears used in transmission systems, engine components, and other critical parts. The automotive industry requires high precision and quality, and the Huge Gear Hardening Scanner delivers.
- Transmission gears: The system is used to harden transmission gears, which are responsible for transmitting power from the engine to the wheels.
- Engine gears: The system is used to harden engine gears, which are critical for the performance and efficiency of the engine.
- Differential gears: The system is used to harden differential gears, which are responsible for transmitting power to the wheels.
Industrial Machinery
The
Huge Gear Hardening Scanner is also used in the industrial machinery industry for gear hardening applications. The system is ideal for hardening gears used in pumps, compressors, and other critical equipment. The industrial machinery industry requires high precision and quality, and the Huge Gear Hardening Scanner delivers.
- Pump gears: The system is used to harden pump gears, which are critical for the performance and efficiency of pumps.
- Compressor gears: The system is used to harden compressor gears, which are responsible for compressing air or gas.
- Gearboxes: The system is used to harden gearboxes, which are used to transmit power from one component to another.
Other Applications
The Huge Gear Hardening Scanner can also be used in other industries, including:
- Wind energy: The system can be used to harden gears used in wind turbines.
- Marine: The system can be used to harden gears used in marine vessels.
- Construction: The system can be used to harden gears used in construction equipment.
Overall, the Huge Gear Hardening Scanner is a versatile system that can be used in a variety of industries where high precision and quality are required.
Frequently Asked Questions (FAQS)
- What is gear hardening?: Gear hardening is a process that involves heating and cooling the gear teeth to achieve the desired level of hardness.
- What are the benefits of induction hardening?: Induction hardening offers several benefits, including precise control over the hardening process, fast processing times, low energy consumption, and minimal distortion.
- What is the Huge Gear Hardening Scanner?: The Huge Gear Hardening Scanner is a state-of-the-art induction hardening system designed for large gears.
- How does the Huge Gear Hardening Scanner work?: The system uses a combination of advanced technologies, including induction heating, scanning technology, temperature control, and a cooling system.
- What are the benefits of the Huge Gear Hardening Scanner?: The system offers several benefits, including uniform hardness, minimal distortion, fast processing times, and low energy consumption.
- What are the common applications of the Huge Gear Hardening Scanner?: The system is ideal for applications where high precision and quality are required, including aerospace, automotive, and industrial machinery.
- Is the Huge Gear Hardening Scanner suitable for small gears?: No, the Huge Gear Hardening Scanner is designed for large gears.
- Can the Huge Gear Hardening Scanner be customized?: Yes, the system can be customized to meet specific requirements.
Case Studies
The Huge Gear Hardening Scanner has been successfully used in various industries, including:
- Aerospace: A leading aerospace manufacturer used the Huge Gear Hardening Scanner to harden gears for a new aircraft engine. The system ensured uniform hardness and minimal distortion, resulting in improved engine performance and reduced maintenance costs.
- Automotive: A major automotive manufacturer used the Huge Gear Hardening Scanner to harden gears for a new transmission system. The system reduced production time and costs, while ensuring high-quality gears.
- Industrial machinery: A leading industrial machinery manufacturer used the Huge Gear Hardening Scanner to harden gears for a new wind turbine. The system ensured uniform hardness and minimal distortion, resulting in improved turbine performance and reduced maintenance costs.
Conclusion
The
Huge Gear Hardening Scanner is a state-of-the-art induction hardening system designed for large gears. The system offers several benefits, including uniform hardness, minimal distortion, fast processing times, and low energy consumption. The Huge Gear Hardening Scanner is ideal for applications where high precision and quality are required, including aerospace, automotive, and industrial machinery. With its advanced technology and customizable design, the Huge Gear Hardening Scanner is the ultimate solution for gear hardening applications.
Glossary
- Gear hardening: A process that involves heating and cooling the gear teeth to achieve the desired level of hardness.
- Induction hardening: A non-contact, electromagnetic heating process that uses an induction coil to heat the gear teeth.
- Scanning technology: A technology that uses a scanning device to ensure precise control over the hardening process.
- Temperature control: A system that controls the temperature of the gear teeth during the hardening process.
- Cooling system: A system that rapidly cools the gear teeth after heating.
https://dw-inductionheater.com/huge-gear-hardening-scanner-with-induction.html?feed_id=254214&_unique_id=66c352a150074